Posted on
May 17, 2010 by
bp complaints
New Deepwater Horizon images:
ROV attempting to activate Deepwater Horizon Blowout Preventer

Image by uscgd8
100421-G-XXXXL-_003_-_Deepwater_Horizon_fire

Image by uscgd8
Deepwater Horizon Oil Spill – MODIS/Terra Detail (with interpretation), May 1, 2010
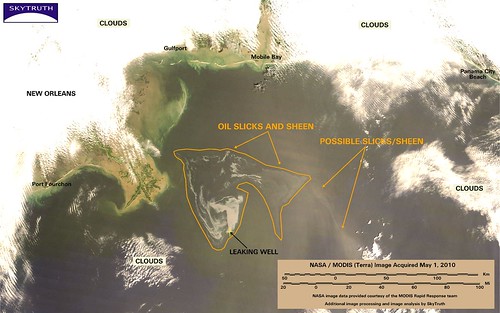
Image by SkyTruth
Tags: Activate, attempting, blowout, Deepwater, Horizon, preventer
Category
News
Trackback: trackback from your own site.
if the shear rams a activated and the blind rams are retracted back in their envelopes then perhaps a measure of the pressure required to extend the blind rams just a little would provide a pressure estimate above main shearchoke (so long as no obstruction directly against blind ram). doing on both sides could provide some correlation.
the blind ram pistons would only have to work against a bit of the pressure in BOP to get a reading.The low flow rate minimises any significant upforce vector on ram reading
a BOP on shore set up with the same hydrallic pressure in the ram could variate the pressure in the BOP until the ram was held in the same equilibrium therefore giving psi estimate in BOP needed
Hector160
The BOP rams are pressure balanced, it doesn’t take anymore pressure to open or close them on the surface than it does at 5,000ft or with 10,000psi in the well.
The best hope for an accurate pressure is to use one of the existing pressure ports. The problem lies in getting an ROV into the area they are located to hook one up.
Subsea BOPS and trees have very few outside connections, that are in contact with the well bore, for obvious reasons, the more holes in something the higher the odds of a leak occurring. Just about every port on a subsea BOP stack is dedicated to a specific purpose, and already has something hooked to it. Possibly when the Discoverer Enterprise gets on location with the oil gathering saddles, they can drop a BOP umbilical down and hook up to the old stack, whether a ROV can disconnect the old umbilical and hook up a new one? I don’t know.
The Development Driller II Spudded the second relief well this morning.
http://www.rigzone.com/news/article.asp?a_id=92524
That makes 2 relief wells now started, the cofferdams for subsea oil collection are supposed to be on location this weekend or early Monday.
http://www.rigzone.com/news/article.asp?hpf=1&a_id=92099
Horizon said:
"The part that concerns me most is as stated before, the riser tube is in severe stress right now, and drilling a hole in it may initiate a crack across the stress zone. The outside of that kink in the riser tube is in severe tensile stress, I for one am surprised it didn’t just split open when it bent over at that angle, hats off to VETCO’s engineers."
This, along with your comments about the capped pressure potentially exceeding the strength of the riser, were what led to my customized "hot tap" idea above … that you build a hot tap "saddle" that is maybe 6 or so feet long – that wraps the riser pipe below the kink and essentially sits on top of the top flange …
This saddle would be strong enough to accomodate the riser pressure once capped
It would also include two hot taps – a lower smaller one would drill a relief/bleed which could be hooked to a separate riser to collect oil and could provide relief control once capped
The second larger hot tap port would be big enough to allow the riser to be cut and plugged with the relief bleed allowing pressure management
Another alternative, instead of attempting to insert a hard block in the top hot tap might be to use the commercial hot tap noted just above … use a ballon plug of some sort to temporarily restrict teh flow … under high pressure this wouldn’t probably work but with a bleed valve already cut in below I would thing an inflaqtable or similar temporary plug would rstrict flow enough that the riser could be cut off flush with the top of my "hot tap" saddle … and the saddle could have a cap designed to be put in place once the riser is cut off flush
link to drawing of my "HOT TAP" noted above
HOT TAP Drawing
220mph,
That would work fine for a round pipe, if you look at the picture in my previous post, the riser is no longer concentric, it is egged because of the kink also if you notice there are 2 3" choke & kill lines a 3" booster line, as well a half dozen or so hydraulic lines you can’t see in the pic they are on the back side, I don’t think they would want to cut these lines, as it may release any remaining hydraulic pressure in the system, without electric power to the Pods they have no idea what position the controls are in.
Most likely they will wait until the well is killed, then the ROVs can use thermal lances or, shaped charges to cut away the junk, before they remove the LMRP.
The real skinny on what happened on the Horizon, that caused the blowout, and the events that lead up to it, this is from an eye witness.
http://www.rigzone.com/news/article.asp?a_id=92765&hmpn=1
There alot of innovative proposals here. For some reason refrigeration appeals to me.
However, deep down I favor pumping. For all of you in the business of pumping oil consider this. Sink a drill bit in the vicinity of the riser approx. 100′ into seabed, just deep enough to anchor a pipe. Attach a pipe to the bit. The first 120′ feet or so of the pipe is solid. Just above the solid section, close to a leak, there is a hole with a coupling to which an ROV attaches a short section of pipe or hard suction hose. Pump the oil/water out using a method similar to what was planned for production. The surface collection methods would be the same as described in previous posts.
My questions are: 1) how fast would the oil/water be coming out of the end of the pipe at the surface? and 2) is a deepwater rig required where you are only going to drill a shallow hole such as this?
This may or may not have been covered already as I have not reviewed every single post.
I found a few pics of the BOP and if I am correct at what I am seeing, there are already taps incorporated into the design below the shears. potentially these could be used to pump pluggage into the system to stop the flow from below the rams. sounds to easy though doesn’t it.
What about pumping huge amounts of lead pellet or buckshot into choke and kill lines?
Until focus stays on choke and kill line and BP has chosen top kill approach I’m a broken record.
ConcernCitizen: I understand your question. There are two separate issues if you will. Scooping/vacuuming the spilled oil and stopping the spill.
All ideas, for Heavens sake, are good. The boxes being made by Wild Well Control, seem to be the best idea so far to vacuum spilled oil close to the source.
The exact answer is 1). Velocity at top would be same as velocity in at bottom if the tubing was the same size at top and bottom. Fluid flow is better described as flowrate at flowrate wouldn’t change as long as the tubing stayed full. 2) yes, you would need a Deepwater rig or subsea intervention vessel. Or similiar vessel designed to work in deep water.
Petroleum Engineer1,
I don’t know if the ROVs can open those valves, there may not be a control for them on the BOPs. And you would have to find a way to tie into the choke or kill lines to pump anything.
Hammer,
Most test ports on BOPs are 3/4" Straight thread hydraulic fittings, with an o-ring stub on the end, the hole it pokes into is only 1/2" ID this stack may be different? without the actual drawings it would be a shot in the dark. Don’t forget there is at least 3,000psi in the stack and if those plugs come loose they will fly like bullets, and may damage the last few threads so nothing could be screwed back in, to plug the hole, assuming you could get anything to go back in with 3kpsi oil squirting out.
Horizon.
In my experience most maintenance people will install fittings and valves on these type ports before installation to accommodate swifter inspections and upkeep. is it possible this was done on any of these,
Not a engineer, but do want to offer in my solution.
A two part collar with two wedges driven by explosive shape charges.
Collars will be positioned by ROV , ROV is only positing each collar will have its own buoyancy device to regulate positioning.
Simple design, with drop in pins to lock two halves together. Fab shop available materials flame cut plates, milled guides, welded together probably ready to deploy in less then 24 hours.
Have a CAD drawing.
Explosives are contained inside and behind rams, no lines running to the surface no weight of hydraulics.
It may not shut off the flow complete, but could reduce flow greatly.
Good luck to us all who have enjoyed our gulf.
Hammer,
Some subsea engineers will put high pressure hydraulic quick couplings on, but they screw together, and I don’t know if an ROV could handle the task, also you can’t put anything through them but liquid because they have spring loaded valves in them, I suppose a person could put some ultra-fastset epoxy through them but it would be a challenge to push it in fast enough to do any good. they are intended for little high pressure diaphragm pumps to pressure test with.
KBW 1.0:
that idea isn’t easily dismissed, except that it would need to be done below the wellhead through many strings of metal casing. The riser isn’t likely to be strong enough for the explosive shear nor internal pressure to hold back the oil pressure from the well. It would be very difficult to get a seal on the two clamps unless welded back to wellhead and if we could accomplish that we might simply do it.
Ive got a question to all of the engineers is the riser rated at 500 psi at sea level or 500 psi with 2200 psi on all sides?
The 2200 psi of the ocean on top helps the burst rating of the riser by that same amount.
Imagine the damage as derating this burst rating of the riser by an as of yet determined amount of pressure as well.
Horizon said:
"That would work fine for a round pipe, if you look at the picture in my previous post, the riser is no longer concentric, it is egged because of the kink also if you notice there are 2 3" choke & kill lines a 3" booster line, as well a half dozen or so hydraulic lines you can’t see in the pic they are on the back side, I don’t think they would want to cut these lines, as it may release any remaining hydraulic pressure in the system, without electric power to the Pods they have no idea what position the controls are in."
So then do a custom HOT TAP that accomodates those lines … so the saddle fits around them … and then install a simple pressure relief/bleed line …. allows them to capture the oil in the riser and pump it thru a new line to surface
If there is a path of leser resistance below/before the leaks its should eliminate or largely diminish the current leakage – and allow oil to be captured and pumped to surface
http://www.scribd.com/doc/30916582/Why-Capping-Method-Will-Work-...
Here you go folks, 4 pages of writing about why I feel the capping method has to work.
I encourage you all to read it, I mean, that is 4 full pages of my writing and I know how you guys love to tear my work up.
So here it is, another chance to bash on me and tell me how fluid flow in a pipe has nothing to do with fluid mechanics, Bernoulli’s eq, energy balances, thermo, etc…
I’m ready for the barrage of ad hominem abusive remarks…
OK going with Petroleum Engineer1’s thinking, what about sinking an overturned supertanker over the well head area while they drill the new wells.
"I don’t think they would want to cut these lines, as it may release any remaining hydraulic pressure in the system"
From what I understand, the Riser is already in two pieces.
And even if it wasn’t, what it was connected to is on the bottom of the ocean.
So where is the hydraulic pressure to be lost?
I’m expecting that they will cut the riser just above the BOP. Probably with shaped charges, and maybe in two places, semi-simultaneously, to avoid whipping the BOP or dropping a big chunk of pipe on it.
If they can put a float on the (probably small) piece of riser that would be cut off just above the BOP, they can float it off and leave the BOP clear to put the caisson over it.
Otherwise, I don’t see how the caisson is going to do a lot of good, with the spread out Riser leaking in at least three places, and highly subject to position shifts due to settling. The caisson is only like what, 15 feet on a side? That isn’t going to deal with the spread out leak we currently have.
It would do a fine job if we cut off the riser at a convenient point and turned three leaks into one.
Go ahead–tell me what an idiot I am. Yer probably right.
"I’m ready for the barrage of ad hominem abusive remarks… "
OK,
Yer ugly, and yer mom dresses you funny!
And get yer kids offa my lawn, ya delinquent whelp! And get a haircut!
[On Edit] And turn down that music!
Kenbobb,
Wait, you’re saying they’re going to try and cut the riser off?
From what horizon said, "They plan to shear off the riser just above the LMRP, the LMRP is hydraulically latched to the BOP stack, an ROV can hot stab the hydraulic actuators and release the LMRP it can then be retrieved, then another BOP with a special adapter on bottom to match the LMRP receptacle on the old BOP stack can be run in and latched."
This won’t work anymore? Are the actuators in a place that the ROV can’t reach? I’ll admit, I have no experience with a BOP. But with my analysis, I disregard what the BOP actually does and look at what is coming out instead. That says a lot about what is going on inside.
"Wait, you’re saying they’re going to try and cut the riser off?"
I think (hope, wish) they will turn several leaks into one. Then a single 15 X 15 X 45 foot high caisson could capture all the leaking oil. To do that, I think they need to cut the riser ahead of the leaks.
I believe other folks who say the riser is likely under huge pressure, so I expect they would cut off the main part (explosively, so an ROV isn’t in harm’s way) so it would move out of of the way, and a smaller chunk to get a nice straight pipe. Probably blast off the big part, and then cut the small part and lift it off.
Then they’d have a single leak pointing straight up. Which the caisson would fit over nicely. And which the differential pressure of the lighter oil would create all the suction they would need to vacuum up all the leak (in fact, I think managing the velocity of the rising oil column could be quite the challenge).
But I don’t know my ass from a hole in the ground on this. I’m trying to understand the situation from what I read here and elsewhere. There could be very good reasons why my understanding is total bollocks.
But it makes sense to me at present, and I put it out there for critique or confirmation.
I don’t know squat what BP and the Coast Guard are actually planning.
And you still haven’t turned down that sinful rock n’ roll music, ya whelp! Put out that cigarette and get a job!
My argument with the high pressure argument is, if its under such high pressure, why hasn’t it blown apart yet? High pressure in our system means a high pressure gradient. That means lots of flow or the pressure is accumulated where ever the choke is. If that choke is in the riser, it would have blown already. If it’s in the BOP, its fine, that can handle 15k psi.
If you guys don’t believe the equations that model the stuff or the laws the govern it, then we need to install a pressure gauge.
I think the very fact that BP was even thinking about installing a pressure gauge shows that they’ve done the calculations like me, and it is a worthwhile effort. They aren’t going to spend the time doing something intensive like that with the ROV if they are 95% sure it is a waste of time or will cause some sort of meltdown.
"Then they’d have a single leak pointing straight up."
This was my exact thought haha. I mean, how practical is a 5000ft in length funnel to cover the entire riser to suck up any leaks in it? That is a major project. What if the area was reduce to directly around the BOP? That makes things a lot easier to manage.
They have to cut the riser the piece they are making isnt 1500 feet tall thats where the kink is . So the bop is pressured by the rig above . oops!!! The riser is really not going to burst till around 2700 psi in the good spot ,not at the kink its stressed there.
Another valid point, "The riser is really not going to burst till around 2700 psi in the good spot ,not at the kink its stressed there."
If the riser really has a choke in it, and pressure is building up behind the choke which is right next to the kink, the material probably fatigued due to bending there. That means it’ll definitely blow at a pressure less than 2700psi. But it hasn’t failed, otherwise the riser would blow apart into 2 pieces and our current situation would look like a giant chimney on the ocean floor.
No matter how many times the rov tries to close the rams there is no pressure no to activate it . Why wasnt we informed or is there one way valve to stop it from loosing pressure ? Give us prints not little drawings. Why isnt the bop operated off the well head pressure? It should be self contained. There picture slash drawing says the kink is at 1500 ‘ above the bop or sea floor.
So wait a minute, let me get this straight. In normal operation, pressure lines run from the rig to the BOP to open and close rams. But now those lines are obviously blown off. Now when the ROV gets in there to try and activate the rams, there is no pressure to activate them. Yeah, it seems like there is no fail-safe built into the BOP to provide emergency pressure. I mean, weren’t these sorts of emergencies planned for before hand? It seems like they have a plan A, try to shut off at the BOP which hasn’t worked, but their plan B wasn’t ever in place to begin with. It is more like a scattered effort to just contain the mess, not fix it. The relief well is going to take a while to get up and running, its not a quick fix like we need. I’m sure this accident will lead to massive overhaul of regulation in the industry. They’ll probably have to use dual BOP’s in parallel or something from now on.
thats what kenbobb says. its all top secret im going to bed i hav to get up in 4 hrs
220rpm,
Here are some pics of what this marine riser looks like, if you look at the center hole in the "Spider" that is kinda what your saddles profile would have to look like, but it would also have to seal.
valvcon-hydril.com/_pdf/pressureControlBrochures/VG_hmf_m…
Hoodyz,
There are 4 redundant systems on the BOP stack 2 systems in each control pod there are 2 control pods a "Yellow" and "Blue" also on board the stack is a seawater powered hydraulic pump with 4 redundant pumps on it to power the systems, there are dozens of accumulators that hold ample hydraulic pressure, and volume.
You have not paid attention to the releases coming from BP, the rams work just fine, there is a problem with the pipe in the BOP the shear rams can’t shear it because a) there is a tool joint at the shear rams, which they are not designed to cut, b) the drill pipe is forced off to the side of the stack and the rams can’t force it to the center, they were designed to function with pipe being with a reasonable distance of center.
The BOP is used in emergency situations, and should be prepared for any scenario it might encounter. A tool joint seems like a pretty good possibility since the drill pipe runs right through the BOP. Obviously this was ignored when the design of the BOP was engineered. When designing such an emergency system, you have to take in account any possibility, e.g. tool joint, and invent something for your system that will take care of that possibility. You can’t rule out any possibilities when designing an emergency system, even if the tool joint only has a 1% possibility of being in the location of the shear ram. You ignore the possibility and you end up with accidents like this where by some slim chance the tool joint jams the ram. You have to ask all the "what if" questions when designing emergency systems because those "what if"s can become reality before you know it.
When the engineers screw up design, this is what happens. Now you got the government coming in and clamping down on every move you make. BP is getting eaten alive with costs to clean this thing up along with the lawsuits and Congress hearings that will take place for the next 10 years. I mean look at the Valdez, the lawsuits are still going on today and Exxon is still raked over the coals. Doesn’t exactly help the ‘drill here, drill now’ campaign either when you have 11 guys dead and a marine disaster. But I guess the coal industry isn’t doing much better with their mine accidents.
So Horizon 37 you are saying the rams are stroked to their full length ? How can that possblly be ? And you know they are at full pressure ? Just asking questions
Horizon …
Question 1 … why couldnt you simply have the ROV snip the external stuff on the riser tube out of teh way to allow a HOT TAP saddle?
Question 2 … I see the "Mud" "KILL" and CHOKE valves in this drawing:
http://www.theoildrum.com/files/blowout%20preventer.png
It would appear these connections give access to the riser stack … why couldn’t ne of these be utilized in some fashion to hookup a bleed line/new riser … obviously they are much smaller diameter but it seems they could capture a significant protion of the oil and by minimizing the pressure inside the riser by diverting oil in the riser to a new pipe it could minimize or eliminate leakage at the breaks and kinks in riser?
Question 3 … in your link there is a large grey "collar" below the spider … this already has sveral "tees" manufactured into it and these tees have flanges designed for a bolt on of some sort … the riser pipe is inside this collar … why couldn’t a fixture be designed that would bolt to the end of one of these "Tee’s" that drilled the riser pipe and inserted a tap line that again could be connected to a new riser pipe to divert oil insiode riser to a new riser and onto a containment ship of some sort?
They said the choke and kill ports were to small . It would be good to see a print . instead of drawings. That way we could see the diminsions.
Page 16 of this document shows an exploded drawiung of the BOP and shears ….
http://www.c-a-m.com/cam/search/showdocw.cfm?col=cicdocs&tb=...
The shear rams are the full width of the riser shaft … I see no way that a riser pipe could get cocked to one side or in any way aligned where the shear rams could not engage it …
this rig also has according to the spec sheet from Horizon BOP’s … if I recall two double and one single Cameron TL …the drawings indicate tehse are in a stacked configuration one above another …putting the shear rams at least several feet apart
It would appear the "joints" in riser are very small – basically a couple collars that bolt together … it would seem impossible for a riser joint to block all of the several sets of BOP shear rams …
I have no idea what other "tools" might be in the well bore but it would appear that neither a misaligned riser pipe in the BOP bore or a riser pipe flange could block or affect all of thye several BOP’s
It would seem – especially based on reports of failures in deep sea locations – that while the BOP shear rams may have actuated properly in a test without load (I assume there is NO actual crush test of riser pipe – rather simply that they cycle the rams and determine they respond to commeands) that they did not have sufficent power to shear the riser pipe …
Dear Obama

hdbob,
They know how far the rams stroked by watching the amount of fluid from the hydraulic reservoirs, it takes exactly 11 gallons to stoke any of the pipe rams one way, they all have the same sized hydraulic pistons. They know the hydraulics to the rams are fully charged with the correct pressure, and they know all the rams work, they had just finished pressure testing the BOP stack. This is not a new ball game these BOP stacks have known and proven performance capabilities they have been used for decades.
I used a tool joint in the shear rams as a possibility, it could be the BOP test plug that they were retrieving at the time of the blowout, in either case the BOPs aren’t designed to cut through steel that heavy, if they put a set of hydraulics on the stack that would shear objects with steel that thick it would deform the stack body its self.
BOPs are not nor will they ever be designed to function properly without a rig or some other means being able to move the pipe up or down and keep the pipe vertical in the stack.
The choke and kill lines are 3" ID, You can’t just pop a hose on these lines they are a special slip together design, and a special adapter with a means of holding the attachment together, besides there is no way of knowing if any of these joints are still viable along the length of the riser, it just fell 5,000ft and is broken in at least two spots that they know of.
220mph,
I think you are getting your terminology a little mixed up, the the riser is on the outside of the BOPs it is the 21" pipe that runs from the BOPs to the surface, and those small collars you are referring to are 40" in diameter and about 8" thick each, the bolts that hold them together are 3-11/16" OD, they are made to withstand a pull of over 3.5million lbs.
What is in the BOPs is drill pipe, it’s not clear what size it is, I am sure that information will surface eventually. But just assuming it’s 5" 19.5lb/ft which is a standard, the tool joints are 7" OD and the wall thickness is a little over 1-3/4" they are made of high strength tool steel, the alloy depending on the grade of the drill pipe body they are attached to, and they are just a few degrees softer than a high speed drill bit you would find in your shop.
Horizon
Mornin. you told hdbob that the choke fittings are special fittings. you aren’t saying that someone was foolish enough to use special fitting/ quick disconnects I`m sure. without check valves built in? I find it hard to believe. if the fittings had no check valve built in it there is absolutely no reason to use "slip together designed fittings"
Hammer,
These fittings are held together by the riser bolt flanges along the length of the riser, the bottom connection at the LMRP "Joint #1" has flex lines, that are held together by high pressure bolted clamps. The connections from the LMRP to the stack are covered by a protector when the LMRP is detached from the BOP stack. At the top of the riser is a ring that has all of the connections for these lines on it, it bolts to the last joint which is the slip joint, and there are flex lines from there to the rig.
Here is a cutaway of what choke or kill line connector looks like:
http://www.freepatentsonline.com/6623044-0-large.jpg
They don’t put stab locks along the length of the riser because they restrict flow and would erode away during a kill operation, in which high pressure, high velocity and highly abrasive fluids will be moving through them. Not to mention if one failed or fell apart in the line, it would mean pulling the entire stack back to surface to repair the connector and clean the junk out of the lines.
lol
never mind.. I misunderstood where you were talking about. I was in a whole other world. I need to get some caffeine in me and get my brain running before I let my mouth run.
Perhaps new regulations will require more access with connectable fittings to choke and kill lines and actuators via ROV to surface for an event similiar to this.
Also port with ROV access to cut pipe via jet cutter operated at surface via intervention vessel and depth via ROV.
Should have already been done.
I still feel that injecting a two part expanding sealing foam, sort of like we use for insulating around windows etc. but I do believe there are some that will expand in the oil under pressure. into the line under the bop would work to plug the leak at the restriction under the rams. It seams to me that the flow there should be slow enough to allow for enough expansion for sufficient buildup to plug the leak. it doesn’t take much to plug an orifice as you know. and I think that is the situation of the configuration of what the leak looks like inside the bop. it seams it would be worth trying while the other options are being worked on.
Or if that is not available the liquid nitrogen would still work as a freeze plug.
Petroleum Engineer1
Unfortunately you can’t design a system for a one in a million chance occurrence. It would be equivalent to mandating the installation of an automatic parachute on the back of every car made, in the off chance some duffus would intentionally drive one out of the back of an airplane and need one.
These stacks are already too complex, they require 24hr monitoring by at least 2 people as it is. And remember Murphy is ALWAYS looking over your shoulder, "the odds of a systems failure is exponentially proportional to it’s degree of complexity", and on a subsea stack the more access points there are the greater the odds of a leak.
For heavens sake, I disagree. I think it is a 1/16 chance that a tool joint lands in the shear ram void (32′ jt and 2′ tool jts.~~)
Install a new system where there is an abrasive jet cutter with a fitting a safe distance from rig tethered on a flotation device at a depth accessible by divers. The day of the shear ram for subsea has come and gone possibly.
If a car crash had the potential to do a trillion dollars of damage then, yes, begin installing parachutes.
If the shear rams are truly functional and won’t close due to big OD steel at shear ram height, then chain drag riser and try again while doing so until steel of minimum OD is at shear ram height and they successfully sever a section and close.
Are they fretting over releasing a substantially increased amount of flow while doing this? Simply waiting to position a suction can over the spill plume? Or the relief well intervention(s)?
Anyone know?
I suggested that yesterday. upping pressure if possible and working rams to try and achieve minimum flow. I would hope that was one of the first things done if if is possible.
if there is no backup hydraulic system, there should at least be some backup accumulators, I would hope there are several redundant hydraulic supplies. if not, someone needs spanked IMHO.