Posted on
May 17, 2010 by
bp complaints
New Deepwater Horizon images:
ROV attempting to activate Deepwater Horizon Blowout Preventer

Image by uscgd8
100421-G-XXXXL-_003_-_Deepwater_Horizon_fire

Image by uscgd8
Deepwater Horizon Oil Spill – MODIS/Terra Detail (with interpretation), May 1, 2010
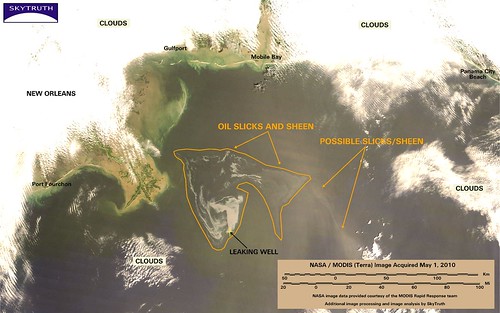
Image by SkyTruth
Tags: Activate, attempting, blowout, Deepwater, Horizon, preventer
Category
News
Trackback: trackback from your own site.
This is what we know so far. BP is building cofferdams that will be connected to pipe which will pump the oil to a processing ship above. So we know there will be lifting equipment and pipe joined at or near the site. Knowing this equipment is available should spur some new ideas. Keep them coming and don’t be timid if you have a sound idea. This forum has been impressive. Brainstorming has provided quality ideas but these will go nowhere unless you submit your idea to BP. To submit alternative response technology, services or products please call (281) 366-5511. If you are unable to get through email your idea/products/services to horizonsupport@oegllc.com
By the way, why on earth would you say this:
"Do a simple test designed for simple people, go out and hook up a garden hose turn it on an pinch it, what do you suppose happens?
I will tell you, the pressure increases behind the pinch the velocity increases in the pinch and the pressure drops downstream of the pinch."
The pressure is at P1 before the pinch and velocity is V1. In the pinch the pressure is P2 and the velocity is V2. Downstream of the pinch, the pressure is P1 and velocity is V1. Pinching has no effect on P1, only P2.
Quite literally, this shows your lack of fluid mechanics knowledge all together. I mean come on man. No more touting your BSME. It is time to head back to school.
Still think I’m wrong? Ok fine, simulate it with the below link.
home.earthlink.net/~mmc1919/venturi.html
Time to pull out the childish examples, I mean come on man. Your down to just blatant mistakes. Please just lay off the posting for a while and dig out the fluids book. Leave the engineering to the big boys.
P.S. Don’t go and edit your post you wrote and try and act like I’m making this up. I have a screenshot to prove exactly what you just said. You go and change your words around and it isn’t going to look very good on your part. I mean talk about the glove being a perfect fit, you just demonstrated you don’t even understand the most simple problem in fluid mechanics. This glove fit so well, it proves without a reasonable doubt that you aren’t qualified to be discussing the capping process.
Remember your idea may help save the coastlines, wildlife and a way of life for the people of Louisiana, Mississippi, Alabama and Florida. If this oil spill continues for months it would take decades to recover and some areas may never recover. I’m a Louisiana resident and I live near the coast. I appreciate your ideas and help.
Hoodyz
There some irrefutable facts in this world, and equations cannot explain them with any degree of accuracy, empirically proven data beats theorem, every time.
Evidently you don’t understand hydraulics, the speed of a fluids flow downstream of a restriction has every thing to do with the pressure behind it, if it’s restricted by an orifice a fluid can be at 3,000 psi behind the orifice but at atmospheric downstream. Just like the previous example of the water hose, if you cap the end while the middle is pinched off to restrict flow the pressure will still equalize as long as there is flow through the pinch, it just takes longer to do so. And no amount of summation or theory can prevent it.
The pressure that drives an oil or gas well comes from whatever of several methods that drive it, predominately that is water pressure from underneath it. The global average for this pressure is 0.47 to 0.5 psi per foot of depth, there are exceptions, where the formations are geologically active, or have been in the past to cause a higher pressure.
The wellhead pressure is whatever the bottom hole pressure is minus the hydrostatic head of the fluid, if the bottom hole pressure is 10,000psi and the hydrostatic is 6,000psi the static well head pressure is 4,000psi.
However in the case oil & gas wells and to an extent artesian water wells the bottom hole pressure changes with production rate, as the well bore will deplete the near bore pressure faster than the driving mechanism can keep up and the new oil flows through the interstitial pore spaces in the formation, this does not change the hydrostatic pressure, as it is a function of the specific gravity of the fluid vs. gravity of the earth, it is always there whether the fluid is moving or not. but if the well is shut it will eventually return to the original shut in pressure, as wells age this time to recover becomes longer and longer, until it is no longer economical to mess with.
In this particular instance we know for a fact that the well is capable of flowing at extreme rates, there is a burned up sunken rig a few thousand feet from the well head to prove it. At the time it was blowing to surface it far exceeded the hydrostatic column of sea water, as eye witnesses saw the oil hitting the crown of the derrick, and it blew for 2 days, more than enough time to unload all of the drilling mud from the well bore. Crude oil averages about 6.5ppg some are lighter some are heavier. this equates to about 0.34 psi per ft of depth hydrostatic. The wire line tests they did have not been released so the reservoir volume is not known to us, it could be 10s of millions of bbls, also the exact formation pressure is not known to us. But we do know the well blew out and we can approximate within a few psi of what it needed to be to do so. the reason it’s not flowing full tilt now is because its outlet is confined by 2,200 psi of seawater pressure, and obstructions in the riser and possibly the BOP stack, there could also be collapsed casing down hole, which is not uncommon in cased blowouts like this one, because the casing up hole was never designed to have light weight oil in it as opposed to a weighted completion fluid.
ricjames1,
You give me the phone number of one of the BP engineers solving the problem and I’ll call them with my calculations. We need to get straight to the problem, quit dilly-dallying around with all these unfounded arguments and cap the pipe once and for all so the oil stops flowing immediately. I understand your anxiousness to get the problem solved, but we are bogged down in the mud back here with constant argument because some people refuse to do their homework and sit on here bashing others ideas with no backup except flawed examples and numbers that come out of no where. My ultimate comeback to them is, how do you guys know the pressure is so high. You seem to certain that ‘it just has to be’, well then prove it.
hoodyz: If you step on a hose, or kink it, you bet you can reduce the flow. Just try it. If you step on it hard enough, you can stop the flow entirely. Kink a hose and watch the flow out the end reduce. This is the situation we have now. Put your thumb over the end of the hose and you will feel the pressure rise until you can’t hold your thumb there. The pressure buildup will blow your thumb away from the end of the hose, just as the pressure buildup in the riser will blow away the riser.
You are right when you say, "the well is already essentially capped by itself." It is essentially capped at the BOP, or where ever the main constriction is, but not at the riser or the hole in the riser. Cut off the riser and cap it, and then you will have a capped riser, wherein the pressure will rise to the full well pressure. If the riser pipe cannot withstand the well pressure, the riser will explode.
"Just like the previous example of the water hose, if you cap the end while the middle is pinched off to restrict flow the pressure will still equalize as long as there is flow through the pinch, it just takes longer to do so. And no amount of summation or theory can prevent it."
I suggest you run the simulation in that link time and time again that I gave you, because what you are saying goes against Bernoulli’s equation and Q=V*A. And buddy, if you are suggesting it is wrong, you have quite a bit of work ahead of you to prove it. I’m awaiting your publication in ASME journals because it is going to be revolutionary. Although I won’t hold my breath, it might be quite a while before you manage to prove it incorrect.
Okay hector160, I buy that the oil will slow and clump in the netting and result in it backing up so what if the netting is in the form of a loop that is continiously being circulated from the bottom to the surface dragging the oil with it? At the surface it can be wringed of the oil before it is returned to the bottom.
TMM16,
"This is the situation we have now. Put your thumb over the end of the hose and you will feel the pressure rise until you can’t hold your thumb there"
This is correct, but the well pressure is almost equalized with the hydrostatic ocean pressure. If it wasn’t almost equalized, the velocity would be much higher. Can you not understand this? It isn’t like the pipe is gushing oil at a high velocity, yes that would be hard to cap, it would probably blow the pipe up. But its not moving fast! Indicating the pressure gradient to induce flow is relatively low.
TMM16,
"Cut off the riser and cap it, and then you will have a capped riser, wherein the pressure will rise to the full well pressure."
Take your system to be the pipe below the BOP and the pipe above the BOP.
Flow rate in=flow rate out otherwise, you’re creating mass somewhere.
No accumulation, where would it be accumulating in a BOP? Answer that? No generation or consumption, how could there be, no reaction.
All the BOP acts like is another kink in the line. Run my simulator. kink the hose down in the middle and watch the graph. The BOP acts like a kink in our system.
Since the flow is essentially stopped above the BOP, the velocity is very low. It is almost capped already. The flow is so slow, .1 m/s, think about that, really think about that, and that is with 400k gal/day.
Do you realize the pressure drop inside of the pipe associated with .1m/s? It is 4 Pa. If you stop the flow all together, your pressure drop term goes away, and your riser sees a 4 Pa increase in pressure.
The only way your wellhead pressure would start creeping up to blow the riser apart is if you stack dirt on the ocean floor to increase the pressure.
This is essentially an energy balance. In the current state we have some pressure or energy that is pushing the fluid through the pipe.
When the fluid increases in velocity, energy is converted into kinetic energy in the moving fluid and that is why you have a pressure drop inside a pipe. It is the most fundamental concept of fluid mechanics. Go ahead everybody, deny it happens and publish your work, but don’t spend to long on it or you’ll be dead before you know.
If the fluid has nearly no velocity, almost none of its energy is kinetic, so almost all of the energy is contained in the pressure term.
(m*v^2)/2 when the velocity is .1 m/s, go ahead and see how small the kinetic energy term is. This means 99.9% of the energy is still stored as potential or in the pressure term.
So whether the velocity is .1 m/s or 0 m/s, it is not going to make much difference.
Energy must be conserved, so what you are proposing is that when the flow stops, all of a sudden energy is being created somewhere in the system to create higher pressure, besides the pressure drop, which is negligible.
Do the balance for yourself, if our velocity is so small, calculate the fraction of the total energy that is stored in kinetic form as compared in the potential form. Why all of a sudden when you cap it, it is going to explode is beyond me! The well is already essentially capped!
If you think the kinetic energy term is incorrect or conservation of energy is false, get to work, because I’m awaiting your publications.
And for you horizon, being a thermo minor, I figured you would understand this concept. So so so simple. Energy conservation my friend, first disprove that, and then you probably got the Bernoulli equation proven false. You’ve got a lot of work ahead of you, not me. Mine methods have been proven. They are in every single library in the world. Your methods exist in our parallel universe.
Here’s another idea. How about a cable anchored to the bottom with a large weight that has a anchor point that can spin freely. The cable is positioned so that the leak contacts it and the cable is spinning. The spinning of the cable attracts the slightly less dense oil to cling to it and forms a inside out conduit for the oil to travel to the surface at one location where it can be contained and remove into barges or ships… Might be a far fetched idea but this is what brainstorming is about…
hoodyz: I think what we have on the seafloor out there is choked flow. See en.wikipedia.org/wiki/Choked_flow When these conditions are reached, no increase of upstream pressure or decrease of downstream pressure will change the flow rate through the orifice. With a very small orifice, the flow rate is small, as you say. But cap off the downstream pipe (riser in our case), and the pressure will increase to the full well pressure. Just like the garden hose.
Hoodyz, if your simulation does not show the pressure equalizing your equation is fubar’d.
If you can not make your formula match real life, the formula is WRONG not the empirical facts.
GO ahead and call BP or any other engineering company, don’t be surprised if they start laughing and hang up.
If you people are unwilling to follow the laws of mass conservation and energy conservation in your calculations, then you are disobeying the laws of the universe. Nothing I can say will sway you. If you can’t be swayed with the most general and fundamental concepts of the universe, nothing will change your logic because essentially, you are wired incorrectly to be doing engineering problems. If 2+2 does not equal 4 in your mind, there is nothing I can do to sway your thinking. You have a mindset and you are sticking with it.
"Never try to teach a pig to sing; it wastes your time and annoys the pig."
Horizon, you are the pig. You can stick around and answer questions about the design of the BOP which you seem to have knowledge of, but when it comes to anything else, just sit back, watch and learn.
I think it would be easiest to collect the spill from the plume on the surface.
Someone said the plume is several thousand feet across, and moves around.
It may be too late for this spill, but it needs small tankers (maybe 30,00 bbl) with multiple tanks to suck up large quantities of oil and water (probably mostly water)
When the mixture fills one tank, the inflow moves to the next tank. While the second tank is filling, the oil in the first tank is drifting to the top. Pump the water out from the bottom.
Oil and water will separate themselves because the oil is lighter.
Some large jet drive catamarans move enough water to fill an olympic swimming pool in 5 seconds. A pump like that would be handy.
It also needs a system of floating suction heads to suck up the surface water. Perhaps strings of suction heads pulled around by a smaller boat at the far end.
It would help if we had a more substantial system of floating dams to contain the spill to a few miles in radius. It should have barriers high enough and deep enough to act like a tank and really contain the oil, not just float on top of it.
A phenomena to keep in mind… if a flat, floating wall is insterted into the water and the bottom of the wall is below the root of any approaching wave, the wave will reflect off of the wall without imparting any energy to the wall. the wall would only have to withstand the weight of water on one side.
Once again, your statements come with absolutely no backup proof. Show me all these fluids textbooks where the pressure equalizes. Show me publications of this shown in real life. Experimental data, there must be some in order to back up what your saying, it has to be somewhere. It is not for me to prove to you that my equations are right, it is for you to prove that your equations are correct. If Bernoulli is wrong, then why is his equation in textbooks? Why is it used anymore, I mean according to you, its wrong. You must prove to me that your theory models reality, and I have yet to see a single link out of you from a reputable source that proves what you are saying is correct. It violates both mass conservation and energy conservation.
hoodyz should take his own advice.
Gentlemen, let’s continue this discussion in a civil manner and ignore incorrent fluid mechanics.
But for now, it’s late and I’m going to bed.
Munson, Bruce. Fundamentals of Fluid Mechanics. 5th ed. Ames, Iowa: John Wiley & Sons Inc., 2006. 112. Print.
I suggest you go and look at this source above. You might just learn something. As a matter of fact, since you are so smart at thermo, they even have an entire section to deriving the Bernoulli equation from the first law of thermo. Oh wait, you don’t follow that law, whoops, should have remembered I’m dealing with the person who isn’t wired correctly. But you might want to check it out anyways on page 236, so you can laugh at how stupid their mistakes are. But I guess there is a more telling question, can you actually open a book, or have you not been trained to do that yet.
Hoodyz,
If you get through to BP let me know, I need a good chuckle.
TMM16,
"Gentlemen, let’s continue this discussion in a civil manner and ignore incorrent fluid mechanics."
If we ignore incorrect fluid mechanics, then basically forget sealing up the BOP, that operates on fluid mechanics. Forget capping the riser, that operates on fluid mechanics. Sorry but ignorance isn’t tolerated when solving engineering problems of such magnitude.
Still waiting on your proof horizon, haven’t seen it yet. It has to be out there somewhere, I’m waiting. I’ve got my sources. Where are yours? If this isn’t an civil way to handle our conversation, TMM16, then you tell me. I reference a reputable fluids book, he refuses to look, and won’t show me anything and instead laughs. I’m waiting…………..
Until you come up with some reputable source to reference regarding your ideas horizon, your thoughts are unfounded and baseless. Where are those references? You can talk the talk, but can you walk the walk? My reference does the walking for me, 816 pages worth of walking.
Hoodyz, Horizon, everyone:
You are all clearly talented and intelligent people. This discussion has a tremendous amount of helpful information and is now at risk of being polluted with name calling arguments.
For respect from those that lost their lives, the ecological damage that is being done, and all that is at stake can we please continue in a spirit that is helpful?
http://www.amazon.com/Fundamentals-Fluid-Mechanics-Bruce-Munson/...
Here is the link for everyone, go ahead, buy it everybody. I want everybody to see my reference. No smoke and mirrors here. It is a readily available book, well reviewed. I encourage everyone to read through it as I have, especially pages 112 and 236. For those of you who don’t have a thermo background and want to learn more in that subject:
http://www.amazon.com/Fundamentals-Engineering-Thermodynamics-Mi...
ThinkAhead949,
As far as this conversation, I proposed an idea. Horizon said it wouldn’t work. I asked why, he has yet to give me any professional referenced answer. For whatever reason, he prolongs this process of problem solving by delaying the revealing of his references. Trust me, if they are out there, I want to see them because then I’m wrong. But if nobody can prove me wrong with significant proof, then I have a potential solution. Horizon is acting to delay any sort of action that might be taken to further progress this idea, similar to a filibuster. We need a fix right away, and he is blathering on and on and I continue to have to disprove every single thing he says, otherwise uninformed people start believing the stuff.
When I try to blow up a balloon with a hole in it, I notice that it’s easy to expel air. When I plug the hole in the balloon, it’s not only more difficult to blow through it, but something makes it expand. The more I blow into it, the greater it expands, but at some point, a new hole appears very rapidly, and once again, I can freely blow into the balloon.
Does anyone know what causes this? Any guess, hoodyz? What cases my sealed balloon to expand?
Also, does anyone know if a kink in a pipe is conducive to laminar flow? When I squint my eyes and stick out my tongue, I can almost imagine turbulence.
When I put on my Giant Asshole hat, I forget all about turbulence, and never even consider it in a long tube and that somewhere along its length there is a standing wave impeding flow.
Well I feel the elasticity of the balloon has something to do with it. With a hole in it, you are blowing air into the balloon which comes out the other side. When you seal the hole, you are pushing in mass to expand the volume of the balloon, which the material resists. This means when the balloon is let go, there is a pressure of balloon material exerting inward, and a lower pressure outside the balloon. By blowing into the balloon, you are providing the work necessary to stretch the material. The material stores this potential energy and then releases it when you let it go, "energy minimization".
I believe there is an energy transformation from potential energy in the material of the balloon which is converted into a pressure energy when it has a chance to flow down the energy gradient, thus expelling the gas you put inside the balloon and causing it to fly.
The difference in our pipe situation is, the flow into the balloon is basically zero, and the flow out is basically zero through a very small hole. If you cap that hole, the pressure will equalize with whatever is in your body. Now considering you are were nearly done blowing it up, and the flow rate was minuscule, the pressure is very close to equalization pressure. That is how our situation is current running in the pipe. If you do the calculations, the current pressure drop due to its low velocity is somewhere between 1-4 Pa, very small. But it makes sense, because if there were a larger pressure gradient between the well and ocean, we would have more flow=more velocity, and we don’t seem to according to BP estimates. So the pressure in the well must be very close to the pressure in the riser already because the flow is so little. Capping it will introduce only a tiny amount of pressure increase, no where near the 600psi that everyone was talking about.
Hoodyz,
I explained to you why it wouldn’t work, you fail to grasp it.
Do you know what a pressure regulator is?
I will try to explain it as simply as I can. It’s a pressure controlled line restriction or valve. Some pressure regulators are actual crimp devices on tubes, a perfect example is the regulator in a kidney dialysis machine, it has a small roller that pinches down on the blood tube to regulate the pressure returning back to the kidneys so that they don’t rupture.
Another is the fuel pressure regulator on your fuel injected car, it is set to maintain 17psi at your injectors regardless of how much fuel you use or how high the fuel pump pressure is.
The perfect example in this case is a partially closed valve, the pressure behind the valve is 70psi the pressure down stream may be 10psi flowing and the flow is reduced, however if you put a cap on the hose the pressure in the hose will equalize with the pressure behind the valve at X rate until flow stops. I could put down a mathematical formula for it, but why bother? common sense rules over estimations of a formula. Besides it is only useful if you are doing a design for the entry orifice of a pneumatic or hydraulic timer.
fbrad
Re your idea
would need a oil material sufficent to withstand that seapressure provide sufficient absorbant/attraction properties to hold onto the oil(bearing in mind seawater molecules a smaller than oil so would penetrate any substance first)and not dislodge by downward sideway forces
NB a house plumbing valve reduces the pressure at the taps from the council main permanently by restricting the flow with a valve that just reduces flow channel diameter only using the diaphram spring to change valve position if mains pressure changes. The house taps dont need to be regulated to main/prehouse pressure when closed
Think about it like this. The higher pressure inside the balloon when sealed up and tied is used to hold the material in place from deforming. It is essentially in a state of high potential energy and since it is sealed, it stays in that fashion. If you introduce an energy gradient where the energy is allowed to escape by cutting a hole, the energy tends to minimize due to the laws of the universe. The potential energy that is in the material hold it in place, its then converted back into in the form of pressure and it flows out of the balloon to the lower pressure/lower energy, thus emptying the balloon. Does that make sense?
What you say makes sense:
"The perfect example in this case is a partially closed valve, the pressure behind the valve is 70psi the pressure down stream may be 10psi flowing and the flow is reduced, however if you put a cap on the hose the pressure in the hose will equalize with the pressure behind the valve at X rate until flow stops."
But what if the pressure behind the valve is only 11psi and the pressure down stream is 10psi. Then the pressure increase when capped is 1psi. So if your equipment could handle 1psi increase, then what is the big deal?
Your definition of pressure regulator is also incorrect.
encyclopedia.thefreedictionary.com/pressure+regulator
A regulator has an ability to shut off flow. A crimp doesn’t.
Secondly, a crimp only reduces the area for flow. Q=V*A
The flow rate has to be the same on both sides of the crimp or you are building pressure on one side which will eventually blow up due to accumulation of pressure. It is an unsteady state system you are dealing with.
So essentially a crimp increases velocity while reducing area. The pressure directly at the crimp will be reduced due to Bernoulli’s equation of flow. Increase velocity, decrease pressure. Same vice versa. It is an inverse relationship. Energy of the system has to remain constant. If pressure energy goes up, velocity energy must go down. But flow rate remains the same, mass balance on the pipe. It has too, otherwise you are accumulating mass somewhere, and it is going to build up with time, it is not steady state.
If I increase the pressure put on the end of the pipe, it will always increase the flow using a crimp.
When you say "Another is the fuel pressure regulator on your fuel injected car, it is set to maintain 17psi at your injectors regardless of how much fuel you use or how high the fuel pump pressure is."
This could not be done with a crimp. If I increase the pressure in my fuel line to 5000psi, you’re telling me the crimp works for all pressure differentials and always outputs the same pressure. That my friend, is a physical impossibility. Put more pressure on the line and you’ll always increase the flow rate through the crimp. A pressure regulator, using springs, is able to adjust for differences you might encounter in input pressure, your crimp size does not change size and let alone, does not lower pressure after the crimp. You’ve still got the same amount of energy entering the pipe as you do leaving, just in different forms. Both a crimp and pressure regulator effect on energy distribution, but they do not have the same effect and work in different ways. Crimp deals with changing P and V. A pressure regulator uses a spring to absorb some of the energy.
Same concepts can be applied in voltage and current with resistors. I hope this answers your concerns.
The crimps in our pipe are not acting as pressure/flow regulators. They physically cannot stop flow. If they were doing this, pressure energy would be building up trying to get through, until it burst or equalized. Do a mass balance around the crimp. Min=Mout, Qin=Qout, and if this is not the case, then you have accumulation behind the crimp, mass is flowing up to the crimp but not flowing out. This creates a pressure pocket. This energy must be absorbed by something. And that something is the riser tube. Eventually it will burst due to pressure buildup or until you equalize with the pressure in your reservoir. If the kinks are acting as pressure/flow regulators, and if the pressure were so high like you suggest, they would have already blown apart. Instead the riser remains intact to some extent. This means putting a cap on it, isn’t much different than crimping it even tighter than it is, which at the current velocity shows that it must be crimped pretty tight because its at .05-.1 m/s. That is assuming your crimping ideas are causing the flow reduction. I don’t believe in this, but I’ll go along with it for now.
A cap is another thing entirely separate. If you look at a mass balance on a cap, it goes like this. No mass in = no mass out. So there is no accumulation of pressure in a pocket, it just equalizes right away. It’s purpose is not trying to regulate flow, but rather stop it all together. When the flow stops, the pressure in the well equals the pressure at the cap. But if you look at our situation, the velocity inside the pipe is so low that the pressure inside the well is equal the pressure inside the pipe already. Since the velocity is essentially so close to 0 in the first place, the pressure increase when you stop flow is going to be minimal. Do an energy balance on the fluid. 99.9% of the energy is in the pressure term right now, and .1% is in the velocity term because it is so low (m*v^2)/2. Why is the velocity term so low? Because the pressures are almost equalized between the well and the ocean. If this weren’t the case, and the well had high pressure right now and there was a large gradient, the velocity term would have to be really big to make up for the difference in energy. Very very very little energy is in velocity right now. That leaves only 1 other option for the energy to be stored in. Pressure must be almost to equalization already.
If you can’t understand the last paragraph, I can’t help you. It obeys all laws of physics and makes logical sense.
The pressure is already equalized, the pressure is already equalized, the pressure is already equalized.
So now answer this, if it’s already equalized, then what effect does a cap have? 0. Nothing. Nada. The cap causes equalization, but that doesn’t matter, because it is already at equalization. Or better yet, it is within 4 Pa of equalization. If our riser can’t handle the increase of 4 Pa, we are in trouble.
The key thing is understanding we are at equalization. If we were not there, the velocity would be way higher, and BP’s estimate of 210k gal/day is absolute BS and we are instead at a much much higher velocity, maybe 100x, 200x, the estimated .05-.1 m/s. If this is the case, we are leaking something like 21mil gal/day. If you think BP is that far off on their estimation skills, then you are definitely posing a direct challenge to their engineering team, so point your criticism that way.
hoody your equation relates to pressure at the cap. Put pascals law into that equation for that whole riser length and reevaluate that affect on vulnerable points
Hoodyz,
I don’t have any concerns, how ever you do.
I have tried to explain this in layman’s terms, which you are one. I doubt if you have ever seen a drilling rig other than in pictures or drove by on on a road, let alone been on one.
Your idea of a regulator is incorrect, many regulators are constant flow, or constant pressure they don’t cycle off and on they use a caged valve or a needle and seat type valve to maintain a constant pressure irregardless of flow rate, or visa versa, the gas meter on your house is a prime example. And yes a crimp can be a perfect regulator, by adjusting the pressure on the crimp to either maintain a constant flow or a constant pressure whichever you want.
In the case of this well, the pressure is a given, the well flows from a given depth, the pressure at that depth will be the hydrostatic pressure of the water in the reservoir plus the overburden pressure of rock above it with a few other geology features you wouldn’t understand. This is immutable. the only thing that will change it is if a) the reservoir depletes, or b) the formation gets damaged from chemical or water invasion which plugs it up near the well bore. BP did specific tests using pressure draw down and build up analysis which is proven by years of empirical research, I could put those equations here but they are irrelevant to the job at hand and again you wouldn’t understand them. Any mathematical formula is meaningless unless you know what the variables are and what they function as in the equation and why, and how they interact to effect other variables. The tests that BP performed gave them a very accurate estimate of the physical size (extents) of the reservoir, and a pretty good idea about how much oil is there and how much of it is recoverable. This well did not deplete in 3 days so it is very logical to project that the well head pressures are within the range I have stated. the flow rates may be restricted my mechanical means ie. collapsed casing, partially closed BOP rams, and crimped and collapsed riser and drill pipe. Just because flow is restricted does not have anything to do with well head pressure, because for all intents & purposes it is constant, and as long as the openings are restricted it could well stay constant for 50 or more years. There are wells in the GOM that have been producing fairly constantly since before WWII.
However these steel components will eventually erode from the abrasive action of the flow through them, that is as inevitable as sunrise. And the restrictions will enlarge and the flow will increase, which increases the erosion by the square of the flow rate.
BP has already implement the best plan, capture the oil at the source and pump it to the surface to treatment and storage vessels, drill a relief well and kill the old one, plug it with cement, retrieve the BOPs, cut off and retrieve the well head below the mud line and put a cement cap on it. Then clean up what junk they can off the bottom, and go on to the next well.
the first containment unit to go down over the riser will surely snap it by the kink
relief well near my area at timor sea (montara wellhead) required 5reliefwells
Anyone see a reason why coiled tubing on an intervention vessel guided by ROV couldn’t motor mill it’s way thru and down in or near the closest leak then worm down and inject either hot wax or cement to plug the well? Isn’t this quicker than drilling relief well?
Horizon37: let’s assume the TD mud weight had the well static while running casing so it was balanced at some point. Possibly gas migration doomed the hydrostatic from the liner top would be a good first guess.
petroleum engineer, heat from oil will set wax/concrete in coil before coil got anywhere useful into pipe
No. Hector. Cement is pumped through sea water first; cold. Then oil; hot. The wax sets ip in cold, the cement in hot. Yet retarders are standard in petroleum business. I don’t have time to work through every detail because I’m working on other projects and I’m very busy, yet just sharing thoughts from my own knowledge.
Look. I’ve never tried any of this because the circumstance like this hasn’t presented itself. Another possibility, and then again, we dint know if the choke and kill line can be coonected to or pumped through, is to pump an epoxy; you know the two part chemicals where it gets hard when they touch. Of course if it is possible, and I don’t know this, to pump hot wax you could then pump cold fluid down the opposing line and chill the wax in the wellhead thus forming a plug there. Possible? Yes. Feasible? Not sure yet I’m sure there are smart guys in here that can think this through and tell me. Also I’m not sure if how feasible to get supply of wax nor keep it hot through cold ocean and all the other issues, yet might there be other things to inject if in fact we could intervene somewhere into the riser drillpipe annulus through the closests hole or make our own with a mill and motor held in place with ROV? Sorry for the typing. I’m on my smart phone in a swamp on a rig.
The point is, in well control the key is to have a source anywhere below or at the wellhead to inject anything. Coiled tubing "snaked" down is just that source. Can we put a swell packer on the coiled tubing? Perhaps? Not sure here yet this is not a bad question to ask. If I was a fly on the wall in the office of the task group charged with this surely this would be discussed and either validated or discarded.
must be a effective retarder for a flexi pipe in kinked riser instead of standard casing.
knowing more about the choke kill line status may assist your procedure
I have suggested several times that pumping in an epoxy, fast curing plastic, or even liquid nitrogen to cause a freeze block. what ever is available and feasible below the choke point to try to plug the line. whether a tap or port is available to attempt this is unclear. also can the rov handle this type of operation. plugging the line would be the fastest surest way to get the flow stopped until a permanent fix can be made. But I have not been able to get any confirmed info as to pressures and availability of any way to get it injected. I sure hope someone is looking at this route before things get to bad. anyone can plug a pipe if they try not to. seems everyone may be trying to over think cleanup instead of getting the flow stopped.
That’s right hammer! A subsea intervention vessel has both a Derrick and coil unit. The Derrick can run tubing to keep the coil centered, ROV’s a different depth can keep tubing centered and ROV at some place above wellhead can hold motor with mill still and mill through riser to get into wellhead and below possibly. This is something to attempt while all the other things are being done simultaneously. I, like all people here that know, as said eloquently Hammer, plugging a flowline is pretty easy sometimes.
I hope someone at BP has the sense to gather a team of their millwrights and fitters and let them brainstorm the problem of shutting the flow down. too often the simple fix will be overlooked by stressed out, highly educated engineers when the guys that work with the equipment everyday can stand back and see the forest. the more heads the better. no insult intended to the engineers. just saying that a lot of good experience often gets overlooked.
if the restriction is at the shears and as small as suggested above, and old trash bag shoved in the line below it would seal it up.
Hammer, no offense taken. There are engineers that have a sense of practical reality. Occasionally an engineer with a lab coat mentality spreads his brand of impractical science and calculation or perhaps worse, performance hindering perfectionism. Sometimes field personal don’t see the light as well. I’m also saying that it is possible to mill through the riser without a "tap" with a setup generally described by myself in the comment. Would need multiple ROV’s and a subsea intervention vessel, yet we already have those on location trying to trigger the existing BOPE. There are numerous places accepting ideas to convey to those in charge one: cfrench@innocentive.com
If anyone that can get the best ideas to the command center, they should.
Update on events.
There was a growing consensus yesterday that a tapping point should be drilled into the riser for injection of dispersants.
It seems that this parallel what BP have done, looking at their most recent press release, which says "BP has carried out a second approved trial injection of dispersants directly into the oil flow at a point close to the main leak to the seabed."
They say that this "innovative" solution was arrived at as a result of consultation across the industry last week.
Can anyone through light on exactly what BP and its contractors have done?