Posted on
May 17, 2010 by
bp complaints
New Deepwater Horizon images:
ROV attempting to activate Deepwater Horizon Blowout Preventer

Image by uscgd8
100421-G-XXXXL-_003_-_Deepwater_Horizon_fire

Image by uscgd8
Deepwater Horizon Oil Spill – MODIS/Terra Detail (with interpretation), May 1, 2010
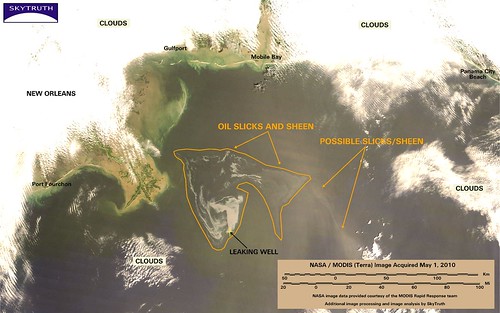
Image by SkyTruth
Tags: Activate, attempting, blowout, Deepwater, Horizon, preventer
Category
News
Trackback: trackback from your own site.
HammerMechanic,
I have been thinking about this for quite a while. I really don’t have a clear answer on this yet. But if we were going to go down that route, it might be hard to get the clot to form because the fluid is still flowing even though it is at a slow rate. Forming a clot in a moving fluid might be hard. But what I was thinking is, it is similar to an artery. Now when eat unhealthy, you have plaque buildup on the inside of your arteries. If only we could inject a chemical that would attach to the pipe wall and eventually build up a plaque that eventually clogs up the pipe. I haven’t done much research, so I can’t really say if its feasible, but it happens inside the human body, be it at a slow pace. The LN2 would be a good idea though. Of course we can’t pump LN2 down for a week straight, but if we were to pump a little LN2, long enough to freeze the pipe for a day, we could pump another chemical in, almost like a glue which would harden up where the flow stops at the LN2 blockage. After this glue is set and hardened, we can stop the LN2 flow and we should have a clot.
rope like material is very good to form clots. try to pump that type material and I guaranty it will find a place to catch. a few steel rods inserted into the pipe could create a good point to begin a plug. but having the capability in place is doubtful. that depth makes everything hard. but I never met a pipe I could not plug lol.
Been thinking along the lines of a crimping/flattening solution (see Bart’s sketch for rough principle) but with a clamp-able sleeve–in two halves–of metal selected for strength but able to deform without cracking. The sleeve would be mounted with its lower end directly on top of the reinforced part of connector flange joint to the LMRP (see Horizon37’s post on the ‘flange designation’).
The idea is to clamp the bottom half of the sleeve to withstand the pressure developed from stopping the flow. The top half of the sleeve would be where the crimping takes place. By applying hydraulic or screw pressure to an appropriately designed, two-part, crimping collar
I am not an engineer so I do not know if this is feasible or even partially adaptable but thought I’d put it out there in the spirit of this thread.
Van der Velden,
They plan to shear off the riser just above the LMRP, the LMRP is hydraulically latched to the BOP stack, an ROV can hot stab the hydraulic actuators and release the LMRP it can then be retrieved, then another BOP with a special adapter on bottom to match the LMRP receptacle on the old BOP stack can be run in and latched.
Before this can happen a deepwater rig has to be put on location, the old junk has to be removed, and new guidelines installed (there is probably tons of debris laying around, like old guidelines, junk that fell off the rig as a result of the fire, and stuff from the deck when the rig capsized). All of these operations are VERY ROV intensive, and ROVs are prone to failure at any given time at 5,000ft, it’s an extremely harsh and unforgiving environment, and ROVs are extremely complex pieces of equipment.
The reason the flow is low is that the riser and the drill pipe inside are kinked, the blowout and fire that was occurring before the rig sank is evidence that the well bore is empty of drilling mud or so much so that it is no longer full enough to prevent production. The reason that the riser has not yet burst is that it is open ended and the pressure is insufficient to cause it damage. Once the riser is capped, it is no longer exposed to the hydrostatic pressure of the seawater, (it becomes a closed system) independent of the depth of the water, this would allow it to reach full wellhead pressure, which is the bottom hole pressure minus the hydrostatic head of the column of oil, which is around 3,000psi, probably more, possibly a little less. The 3,000 figure is based on normal pressure gradients vs depth, if this is an over pressured reservoir it could be much more. It is a given that it is higher than 2,200psi or it would not be flowing, as 2,200psi is the sea water pressure at the seabed. They already know the riser is leaking at the kink above the LMRP, they have video tape from an ROV showing the plume, this could be a large hole under low pressure, or a very small hole under high pressure. They will not get the ROV very close as oil on the ROVs camera and lights would blind it, and operating blind in an area full of junk is inherently nuts, and the only way to clean it off is to return it to the surface.
Horizon37
Thanks for getting back to me. Not a driller, just a lowly geologist (which makes me very familiar with the difference between art and science).
Do you know how far Deepwater Development Driller III’s location is offset from the original location?
Also, most build rates I’m familiar with are in degress per 100 ft. Are you sure about that 1000 ft?
dt.burgess,
I did a typo, sorry I have now corrected it thanks for catching it :-), my KB sometimes has a repeat rate all it’s own.
From the press release I received, the DDIII is around a half mile away from the wellhead. Being that this info is probably 3rd hand I would wait for BP or Transocean to put out a report, before I tried any accurate plotting of the well bore. I am not even sure of the geometry of the Macondo well, it could well be drilled at an offset as well. Which given the terrain they are in is pretty likely as they probably picked the closest flat area to put the wellhead, and drilled a directional well to the target.
Horizon 37,
yfrog.com/744563035602604acffcb1j
Take a look at this modified picture I made. Inside the riser that is within the length I have drawn is what I am focused on. Inside that pipe, from fluid mechanics, the pressure of the wellhead is equal the pressure inside the pipe. The pressure drop due to flow is very low because the velocity is so low. The kink in the line above it is almost acting like a cap. If the pressure in the wellhead were so great, it would have blown apart that riser already. Capping the pipe within that region will make almost no difference in Bernoulli’s equation as shown above. You could not cap it if the pressure differential between the wellhead and hydrostatic pressure were high. But it is low, very low and that is why the flow is so slow. When you cap the pipe, you are closing the system, but you still have hydrostatic pressure pushing on the outside of the riser. Look at the force balance. Wellhead pressure which is at some pressure X. Hydrostatic pressure which is at some pressure Y. The two forces do not equal each other exactly, but they are very close in magnitude. Basically, you are turning the riser into a pressure vessel holding a very small psi differential.
When you say "The reason that the riser has not yet burst is that it is open ended", that doesn’t make any difference on the pressure inside that riser. Sure it is open, but the flow is so slow, from bernoulli’s equation, the pressure drop is comparatively very very small.
If the riser, in the section I drew, has not burst yet, it won’t burst when you close it because P1=P2 already.
Hi everybody, I presented a (very badly drawn) solution that has some advantages over other solutions:
1. It can be made/found within a day
2. It can withstand the huge underwater pressures
3. It gradually shuts down the flow of oil, slow enough to prevent a sudden blow, but fast enough to close it within a day.
http://www.inivention.nl/stop_oil_spill.pdf
Often the simples solutions are the best. Can ANYONE provide a good reason why my suggested solution won’t work?
Thanks in advance, Bart
Bart
Have you check the burst pressure of the riser?
Xray or IR may be able to depict hole size at kink. Since leak and outlet both flow (at similar depth) and riser hasnt collapsed in between and flow at kink is sufficient that they a unsure if kink hole small or large then they must have a wide estimate on risersburst threshold and thus pressure at bop could be rather large still
hoody,
You don’t know what the flow rate or pressure is upstream of the kink, you don’t know how much flow cross sectional area there is at the kink, or the viscosity of the oil at the well head, making assumptions of this nature are exercises in futility at best, no insult intended.
And the rate of flow out the end of the riser and drill pipe is related to the exposure to hydrostatic of the sea water, if this hydrostatic is removed by capping or crimping the tube, as said above it becomes a closed system, the hydrostatic is no longer working on the fluid, only upon the body of the tube, in other words the fluid in the tube will reach wellhead pressure.
Even at a differential of 200psi if they open the area below the kink, an 8.5 inch hole (the ID of 9-5/8 53.5lb casing) the flow could be as high as 30,000bbl per day, and it would make it virtually impossible to cap. As any future ROV work in the area would be over, they could not get an ROV close enough to the well to even get a decent video let alone close enough to work on the stack, the venturi effect from the oil flow would suck the ROV right into the oil column.
If BP is unable to get an accurate pressure reading from below the kink I doubt very very seriously if they will try any sort of removal of the riser or LMRP, before the well is killed, and they will not know the well is killed until the flow of oil stops from the areas it is currently leaking from.
I would say that if the ROVs are successful in getting the BOP stack to function and isolate the well, BP may elect to postpone the relief well, and go ahead and place a rig over the old well and remove the junk and LMRP and set another BOP stack on top, and proceed to kill and recover the well, from there.
If can pump into choke or kill line need to pump fluid to plug line intrigues me at the moment. Don’t know details yet my brain and experience tell me plug the annular flow via junk shot if the pipe rams, annular and/or blind rams are activated yet not completely sealing then if successful follow with an attempt at a top kill via choke and kill line. If these are 3" this is possible. Details of course need mechanical, leadership and G-dspeed.
Hello –
InnoCentive has posted a Challenge about the oil spill – gw.innocentive.com/ar/challenge/overview/9383447. We are working with the White House to get the solutions in front of the right people. We hosted a similar Challenge in 2007 for the Oil Spill Recovery Institute in Cordova, Alaska, with pretty impressive results. The comments and insight on this Flickr stream lead me to believe that this is exactly the right group of people to solve this Challenge and fix this horrific problem.
There’s a blog post about the Challenge from our CEO, Dwayne Spradlin – blog.innocentive.com/, explaining why we’re doing this and what we hope will be accomplished by opening the problem up to the world. It would be tremendously powerful to aggregate all of the great ideas here with those on our site, in submitted solutions and in the discussion board for the Challenge. Please consider adding your solutions to the Challenge on http://www.innocentive.com – we’re confident that we can get them in front of the right people.
Any questions, please contact me at cfrench@innocentive.com.
Connie French
InnoCentive
Anyway…new BOP on top of old one is the final best solution if there is no utility of existing choke and kill line.
From all I have read, I conclude that effectively all (99%+) of the pressure drop and high velocity flow is occurring inside the BOP. As soon as the the riser is capped, no flow though and no pressure drop within the BOP will result in full pressure on the riser and it will burst.
link to drawing of my "HOT TAP" noted above
HOT TAP Drawing
The "HOT TAP" design I did addresses the lower strength of the riser pipe by the HOT TAP being strong enough (thick enough) to increase the burst strength of the riser to withstand being capped …
Effectively the "HOT TAP structure would become the riser and cap by full encapsulating the existing riser pipe above the BOP and below the kink …
The weak point would be where the HOT TAP sits on top of the flange above the BOP but if the HOT TAP once bolted around Riser pipe is allowed to sit on top of the flange the exposed/unsupported riser would be almost nothing … or the bottom of the HOT tap could be machined to fit over the flange somewhat ….
At worst the HOT TAP idea would allow the riser to be tapped and oil diverted to surface thru a new riser pipe … as path of least resistance – and in line prior to the leaks … this would effectively eliminate the existing leaks …
At best the HOT TAP could also be used to cap the riser pipe with the bleed tap being used to regulate pressure when capped …
collar/hottap/psi guage to check psi below kink
hesitant about even a minimal operation on the riser if as horizon says its kinked inside bop
Oceanographers a questioning leakage rate provided (on ancedotal evidence only)
Hi all,
I have been following this post for the past seven day’s now, and it appears to be the only one that has people talking solutions. Thank you all very much.
1.) A deep sea submersible like the Alvin :
en.wikipedia.org/wiki/DSV_Alvin
could be equipped with a hydraulic clamp or some other device that could get under the well head and pinch it off, or clamp it.
2.) Now for the oil coming to the surface.
It appears that the Gulf Stream has the oil spinning in a counter clock wise direction. Why couldn’t a flotilla of boats, pulling a semi submersible barrier in single file be used to corral the oil? I realize that the oil slick is massive, but if you bite off sections that are closes to the shore maybe you could keep it from hitting the shore. If the lead ships have a deep draft (large displacement) that would push the oil into the center of the vortex. If the ships travel in the same direction as the Gulf is spinning the oil, The oil skimmers could travel in the opposite direction in the center of the vortex and suck up the oil.
Here’s a query/suggestion. Can compressed air be blown into the oil leak at its source to speed its ascent to the surface and contain the point of its spread? It may be easier to then encircle the majority of it as it breaks the surface and collect into ships or barges with pumps.
the air will not diffuse into the oil, it will spread it out further.
A ring of oxygen would encircle the oil and collar it upwards but that is not in a situation with transverse seacurrents
scheme proposal
http://www.PROinvention.com/BP-jack-cap.jpg
You fix a jaw on the pipe
Jaw have pivot for putting level with half of cap
You push the level with a jaw for example and so the half of cap close the end of pipe
I can draw the workkable device on solidworks if you want because I’m designer
If the leak is at the middle of the pipe, device work with half of cylinder at the place of the cap
I’m sure that this device is enought robust
we can set it at the top of the bop
Seems all the focus is on trying to get the BOP to work or spend a lot of time making a big heavy metal cap. I suggest total containment is a much more time critical activity at this point. Fixing the problem can wait. Fabricate a fabrc cylindrical curtains 5000′ long and a 3 mile circumference with flotation at the top and weighted at the bottom. Do it now and surround the leak site. Make it larger if necessary. Pump the oil out as it fills the cylinder. take your time finding a final fix (freeze plug is impractical imho, the thermodynamics are prohibitive in that location)
The construction time for one that could handle that psi/length is much more than the current confinement devices in production
Does anyone know the final mud weight while drilling this well? The pore pressure of the producing zone? And or depth of producing sand?
Drillpipe(s) sizes, depth, details? Casing depth(s), details?
Boxitlin _ The curtain would not have to be anywhere near that large, but it would take some engineering to design it to survive. The currents in this area are not real high, but even a 0.5 knot curret on an impermeable curtain 5000′ long would place immense loads on it, and almost certainly would tear it apart before it was deployed. Riser engineers have to design their risers for huge loads, and their pipes are only 36" or so in diameter. And where would you get the material to make it, and who could make such an item before the relief well could be drilled?
The most practical solution is the containment devices BP already has under construction. These should be ready for deployment within a week.
I fear that all the hot stab, capping, crimping, freezing ideas (even if workable) present the very real risk of damaging the BOP more, ending up with an open hole flowing at formation pressure. We must remember that installing any of these devices with an ROV will impart loads, vibration, etc. to the BOP which could damage it more, or knock it over.
It appears that BP is well along toward implementing a scheme to contain and collect the oil issuing from the main leak. Hopefully they will be successful. I propose the following for the remaining leaks:
Place a quickly and easily fabricated "catchment" over the leak.
The "catchment" might be an open ended vertical cylinder of such diameter and height as dictated by the situation at the leak site.
The catchment will be directly supported by the sea bed or by a supporting structure from the seabed.
The bottom of the catchment must be open to the extent that sea water can flow in at a point below the elevation of the oil leak.
The oil leak itself should be near the centerline of the catchment above the elevation of the highest part of any openings at the bottom of the catchment.
At an elevation 12" or more above the oil leak, mount a sufficient number of venturi aspirators to propel the oil/gas/seawater upward at a sufficient velocity to prevent oil from flowing downward and leaking out the bottom of the catchment. The aspirators can be powered by either compressed nitrogen or high pressure water.
Attach a tubular curtain made from a readily available impermeable or nearly impermeable fabric. The curtain will form a hollow tube having sufficient diameter to direct the oil/water/gas mix upward while maintaining a complete barrier between the mix and the outside seawater.
Seal the lower end of the tubular curtain to the top of the catchment.
Circular metal horizontal support rings suspended first by cable from (a) surface vessel(s) and thence from one ring to the next ring descending will be attached to the curtain at such intervals as required to adequately support and stabilize it throughout its 5,000 foot length.
The tubular curtain will discharge the mix into the bottom of a floating surface level container vessel equipped with a stack for venting gases to a safe location and elevation. Possibly it will be advisable to have constantly burning "pilot lights" mounted circumferentially around the top of the stack to prevent flammable mixtures from accumulating.
Liquid collected in the surface container vessel will be pumped into a barge or tanker for further processing and or transfer to the shore.
It may be possible to utilize this concept for the major leakage source should the attempt now under construction fail to work effectively.
To TMM16
if the containment devices dont work (never before done in any water near this depth)- then no other intervention- unimpeded oil until relief well in place.
containment devices captures 85% of oil escaping (Joint Information Centre)
Horizon 37,
You have to understand the very fundamentals of fluid mechanics. This problem is analyzed in such a fashion. Without proper understanding of the physical situation, your analysis is bound to be flawed.
We know the total flow rate out of this oil well to be 210k gal/day according to BP. Pressure upstream has absolutely nothing to do with pressure before the kink. We are talking about sealing this pipe up before the first kink. And by its very nature, with the kink leaking some oil, the pressure upstream is less than the pressure at the kink.
Let us analyze the section of the riser before the first kink because this is most important for 2 reasons.
1. It hasn’t blown up.
2. It is where the proposed operations for capping will take place.
For the sake of making things simpler to understand, we will forget about the leak at the kink because it makes no difference for our analysis. We have 210k gal/day flowing through our pipe. Our pipe is 19in ID.
To give you insight on my velocity calculation,
I took 210k gal/day, which becomes .009200 m^3/sec
With a 19in ID pipe, that is .4826 m
The area of that is pi*(.2413)^2 which is .18292 m^2
Dividing the flow rate by the area, gives you velocity in m/s of .05029.
The kink in our system only changes the area term in that small portion of the pipe. What that does, since Q=V*A, since A is smaller, V is bigger, meaning there’s a pressure drop in that small portion. But it flows right back into normal riser pipe where the velocity once again decreases and pressure increases back to what it is before the kink.
You have to understand this point, when you have fluid flow in a pipe, you have a pressure drop. It’s physics. Unless they are not telling us something, I have to believe the same physics applies at 5000ft below the ocean. At 200k gal/day, the pressure drop inside that pipe is 1.075 Pa, yes Pa, very small. At 400k gal/day, the pressure drop is now 4.25 Pa, very small. If you were to cap the pipe, you would essentially see a pressure increase inside the pipe equal to whatever pressure drop you had previously. At such low velocity, the pressure increase is on the order of 1-4Pa, MEANINGLESS!
You do not have high pressure in that well period. If you did, then either the flow rate would be higher, or it would have exploded the riser due to the tremendous pressure. BP is estimating 210k gal/day. Even at 100% increase, now that is 400k gal/day, the pressure drop is still meaningless and capping it would cause no problems. You prove how 4 Pa pressure increase in that pipe will cause it to fail and you’ll be a rich man.
On to the next fallacy, capping it will increase the pressure in the well. Flawed logic. The only thing that will increase the pressure in the well is adding more dirt to the ocean floor. The correlation between capping and increased pressure is only because your pressure drop term is going away. This argument is only valid if you have a flow that is moving with some significant velocity. I’ve proven above that the pressure increase is literally nothing.
Do a force balance before and after the cap is in place.
Before you have oil flowing into the ocean which is pushed by the well pressure and pushed back by the hydrostatic ocean pressure.
After the cap you have well pressure pushing on one side of the cap, and you have hydrostatic ocean pressure on the other side of the cap. Since the pressure in our well is currently equal to the pressure in the pipe(remember, 4 Pa pressure drop, tiny), if it was going to blow up, it already would have blown up! If you put a cap on it, it is not going to make a difference.
It is like an air compressor tank. Why doesn’t an air compressor blow up when it has 300psi in it? Because the material that the tank is made of has a strength and thickness that holds the pressure in. Your logic is that if we cap it, the inside pressure will build up to something like 3000psi and it will just blow up because the riser cannot handle 3000psi. First of all, the well isn’t operating at 3000psi, otherwise we would have a hell of a lot more oil coming out because the velocity would way higher. Second you are neglecting the hydrostatic pressure on the outside of the pressure vessel. It counteracts the pressure inside. You must look at the pressure differential.
All this stuff about cross sectional area at the kink, viscosity, etc is unnecessary. Total flow on both sides of the kink is conserved. You are changing area and velocity terms that is all. And in the real situation, you are leaking some of the oil there, which really doesn’t make any difference, you’re just releasing some of the pressure there instead of the end of the pipe. If you draw your system, similar to thermodynamics, to be the entire riser, leaks along the riser don’t make any difference. Viscosity doesn’t make any difference either. It doesn’t have any place in my calculations.
If you are going to disprove me, you’re going to need to disprove physics and the laws of the universe. End of point, arguments against capping or cutting the line near the BOP are baseless and unfounded. The riser will not blow up, no way, no how.
In some manner you may be able to create a funnel type system over the leak near depth level then tube transfer it to the surfase for a sucking/skimming action into a caro tanker ship and when settling occurs inside vessel pump out the clean water under the oil on top and continue process.
Second… you may try a large faom type wheel whick when turn un revolution would raise oil from the water and then can be skimmed off the other side into a trough by a squeegee type method.
just offering some assistance before i go broke..
wjn.
also your robotic arm may be pushing a button but is there any electrical current to operate tyhe system it is triing to activate?
wjn 253 218 8764.
WJN
its a hydrallic line with a male connector from the robot entering a female receptor
hector160 – thanks for your response regarding the air into the oil stream. I realize that the oil will not mix with the air but with the ascent of the air bubbles creating an up draft so to speak with their expansion and accelleration would not a majority of the oil be dragged along more rapidly to the surface when exposed to the surface tension of the bubbles? Could this then result in less diffusion of the oil by the cross currents which are bringing it to the surface in a larger area?
PetroleumEngineer1
As to the mud weight, at the risk of being silly, obviously it wasn’t enough.
But it can be worked out roughly assuming the well depth is in fact 18,000ft vertical BML, We don’t know that for a fact it could be 18,000 linear feet but if it’s an offset well the actual vertical depth could be 15,000 or less.
A normally pressured reservoir at 18,000ft plus 5,000 ft of sw would be around 11,210psi this was evidently contained by 23,000ft of mud (18,000ft BML + 5,000ft SWD and was brought in by the loss of 5000ft of mud being swapped to seawater in the riser), that works out to a 9.4ppg balance. We know it went under balanced and oil ended up at the surface with a riser purged to seawater, that is a 244psi head loss at the wellhead. So 11,210-244=10,966psi BHHP, at the moment flow started it was 244psi under balanced, this increased rapidly as mud unloaded from the hole. This indicates the hole was full of 9.4ppg equivalent mud wt. plus or minus a point. Or that the formation was excessively over pressured and the head loss of the riser mud brought the well in.
fbrad46
the oxygen would have some surface attraction to the oil. Surface tension properties caused by different densities (Euler lagrange)means the oil would resist attraction and disperse rather than attract and rise, so quite soon a bubble highway to the surface would develope exclusively
hoodyz_r_us
First of all you’re assuming that all the choking takes place in the kinked riser. Trust me, it doesn’t. There’s choking taking place down in the well as well as the through the BOP. The problem is, we don’t know exactly where and in how many stages. Secondly the WHP is not 3000psi, its a lot more. You don’t go down with a 15,000psi BOP on a 3000psi well. So I think you need to be a little bit more careful about critsning Horizon 37 fundamentals regarding fluid mechanics and listen to what he has to say regarding subsea drilling because that’s where you have a LOT to learn. By the way, the riser will burst if you cap it off! There’s a reason why they use a Subsea BOP on floaters instead of a Topside BOP and the reason is that they can’t make a large diameter high pressure drilling riser.
Hoodyz,
You don’t even have the dimensions correct on the equipment, the riser is 18-5/8" ID it’s pinched and no measurements have been done to the outside, let alone the inside, there is pinched drill pipe in the bend, where it’s located, is anyone’s guess, it could be in one of dog-bones at the edges of the kink in the riser or it could be totally separated below the kink, in either case it’s most assuredly broken as drill pipe will not bend at a 120deg angle and remain intact.
And you sir need to reexamine your post, I have pumped more crap in and out of oil and gas wells than you will see in your lifetime, I have a BSME, and associates in PE, with a minor in thermodynamics. And worked offshore doing it for 25years and another 20 in designing and building fired heaters, waste heat units and power boilers.
Your use of Bernoulli’s equation demonstrates your lack of knowledge of REAL fluid dynamics, without knowing the exact dimensions, pressures and rheologies of the fluids, anything is a SWAG at best. I would suggest you buy and study some literature from API like RP 13D, ASME SecVII on properties of steel cylinders, and a book or 2 on the properties of petroleum fluids and a big help would be Cranes flow of fluids TP 410.
In your estimation of well pressures you are way out of your league. Did it occur to you that the reason the flow is not at full bore is because the riser and drill pipe are pinched? and that the plume at the kink in the riser might be a pinhole with 3,000psi behind it? I explained in an earlier post the joint #1 in a riser package is heavy wall, it’s 22inch OD and 18-5/8 ID its burst and collapse pressures are way higher than the rest of the riser string.
Or do you think BP would piss away millions prepping a well in 5,000ft of water for completion for a piddly 5,000bbl/day? if the production was that low, they would have plugged it and abandoned it without running a liner, and written it off as dry hole.
The fact is, nowhere in that riser is the pressure 3000psi or greater.
Second, there is no choking going on anywhere in the riser, the pressure is almost entirely constant in the riser except in the kinks. Flow in=flow out
Qin=Qout
Vin*Ain=Vout*Aout
There isn’t any choking. You’re not somehow going to restrict the flow because you make the area smaller. No way, no how. There is no choking, none, none, none. Change the area, and the velocity will just change. Its an inverse relationship. The flow rate IS NOT changing throughout the riser.
The simple fact that you guys cannot get around is the flow rate out of that well. Wake up and smell the coffee folks. BP estimates 210k gal/day. I’ve done the calculations all the way up to 400k gal/day. If you’ve got all this supposed pressure, where is it sitting? Surely not in the riser, it’ll blow up. So where is it going? Pushing the fluid? Nope, thats moving at between .05-.1 m/s. If you are so smart and know the situation so well, do the calculations for your supposed 3000+ psi pressure. Give me a flow rate for these pressures. If the pressure inside that riser is 10000psi, I can tell you 200k gal/day won’t be coming out. I suggest you figure that one out, I won’t waste my time proving these blatantly obvious facts time and time again.
Obviously in your pressure values, there is some sort of elevation change that takes place which means that the pressure in our riser nowhere near the values you report to be accurate. By the time that oil enters the riser, it is going to be far below 3000psi.
Just remember this, if you’ve got your supposed 5000psi or whatever you are claiming, and the fluid is moving between .05-.1 m/s, you’ve basically got 5000psi on the inside of that riser, no pressure drop due to the low velocity, and 2200psi on the outside of that riser, that is nearly 3000psi differential on that pipe. It is not for me to explain why this is the case, as I already have above, but it is up to you to explain how the riser is not in pieces all over the ocean floor. You tell me exactly where all this pressure is going and why the flow is so slow. Enlighten me. Tout your experience all you want, at the end of the day, your numbers are a physical impossibility showing a lack of understanding of both the physical situation and the concepts modeling the system.
hoodyz_r_us
The reason the flow from the hole just above the riser is relatively small, and there is relatively low pressure in that portion of the riser, is that most of the pipe passing through the BOP was crushed by the rams. Something caused the rams to not close completely, so a small hole was left there and the oil is getting through it, into the remaining riser. This is called choking. If you cut the riser and cap it, the pressure within the riser will rise to whatever the well formation pressure is. Some have estimated that to be 3000 psi or more. Can the riser take it? I don’t know, but the consensus seems to be that it will not. I don’t follow your calculations, but simple fluid mechanics says that the pressure within a closed container (which the riser will be after it is capped), exposed to a pressure source, will reach the pressure of the source, which in this case is the well pressure.
One containment device is apparently finished; with the Navy etc on station would be pleasing to see it moved with full dispatch.
capping would increase the pressure along the whole riser by that of the sea depth plus the few Pa hoody_r_us calculated and that of the kink if capped too.
regarding stresses on a cylindrical fabric curtain this size, make it longer if necessary…who cares if it distorts, so what if it looks like a wet sock… it’s flexibilty is what will allow it to maintain integrity, it doesn’t have to be super strong, make it out of rubberized cotton for all i care, the oil’s bouyancy will inflate it like a salvage bag enough to allow the oil to rise to a collection point… and, what’s the plan if the metal "canopies" fail, sit on our thumbs til the relief well fails, too? extraordinary situations require extraordinary measures, i don’t think BP has the cash to buy an new ecosystem for the GoM
hoodys
There is certainly choking going on. The well is not producing at its full potential. But we dont know where the restriction is! Lets assume the riser is not restricting the flow at all and all the restriction is in the BOP. In a dynamic condition, there will be a lot of pressure benetath the restriction and very little above (i.e. riser). Now if you cap it off, the pressure inside the riser will be at the formation pressure minus the hydrostatic pressure of oil up to the cap. So the pressure in the riser will increase to its static condition. Now what part of that don’t you understand?
All I have to say is, reexamine your supposedly pressure inside your riser right now. It is no where near as high as you guys think, otherwise you’ll had have a hell of a lot more flow and velocity. If you had any feeling for the physical situation, you’d know that going from 10000psi to 2200psi, a large flow/velocity would be taking place. But it isn’t, get over it.
Q=V*A
Q=V*A
Q=V*A
again and again…
Go ahead, spend your time proving it wrong. Do the calculations for your 10000psi pressure. Enough typing, do it. What kind of flow rates do you get with this pressure differential? I guarantee you its no where even close to 200k gal/day, no where even close.
I don’t understand how capping this increases pressure inside the tube. Sure the pressure drop term goes away and turns into pressure inside your pipe, but that is on the order of 1-4Pa. If you have any marbles left, you realize how big that is.
The only way that the pressure inside your riser would increase is if you packed more dirt on the ocean floor. Plain and simple. That is it. How else is the wellhead pressure going to be variable? Capping this sort of system with little to no pressure drop isn’t going to do a thing. You guys have yet to explain why this pressure will start building up. You just say, I’ve got experience and whatever I say goes, I don’t need to back anything I say up, I’ve got experience. Where is this extra pressure coming from? Thin air? If the pressure is there, then its already inside the riser. For the last time, the only pressure buildup you get in the pipe will be from the pressure drop term becoming 0. The current velocity is low enough that pressure drop is essentially 0! So what does this mean? Whatever pressure is coming out of that wellhead, is currently equal inside that riser!
Pressure DOES NOT increase in our system when you cap it. It can only increase by a maximum of 4 Pa at a basis of 400k gal/day(double BP’s estimate).
P.S. While you are on the task of disproving our physics and mathematics equations, maybe you can rewrite Bernoulli’s equation. For deep ocean, you claim it is flawed and is unusable. So I suggest correcting it and sending it in for publication. I guess the laws of the universe do not hold true for the depths of the ocean. Who would have thought?
Hoodyz,
Get a clue, and put away the crack pipe.
Your lack of knowledge on the subject is almost as astounding as the fact that you’re goofy enough to post it here.
Do a simple test designed for simple people, go out and hook up a garden hose turn it on an pinch it, what do you suppose happens?
I will tell you, the pressure increases behind the pinch the velocity increases in the pinch and the pressure drops downstream of the pinch.
There is no difference to this, than there is pinching and kinking a steel pipe. If you take that same hose and put 2 pressure gauges on it, the one close to the faucet will be higher than the one at the end, if you cap the end of the hose the pressure there will equalize to the pressure at the faucet irrespective of pressure drop, because as flow stops there is no more pressure drop because the fluid ceases movement.
Uless you have the hose hanging off the side of a building then the pressure at the capped end at the ground will be higher because of hydrostatic pressure.
The reason there is no or low pressure in the non-pinched portion of the riser is because it’s open on the end, and exposed to the 5,000ft of head of seawater, which communicates through the fluid right back to the wellhead, if you cap the riser it’s no longer exposed to this pressure and it will try to equalize with whatever pressure is at the wellhead, if the pressure exceeds any of the pressures that would burst the severely damaged riser or it’s damaged components, it will burst.
Hoodyz
Look up HIPPS on the internet. Read about it and try to understand what it does to a production system where the pipeline is downrated compared to a shut in condition which gives the rating of the well and christmas tree. Once you understand it come back to us with your fluid dymnics.
Thanks for your expert opinion hector160. If air bubbles cannot form enough of a attraction to suck the oil along with them to the surface what about a poly net tube extending from the surface that is dropped over the leaks where water can pass through the mesh and yet oil will be more likely to cling and rise along the webbing? The size of the web would need to be small enough to capture the oil but large enough to let water pass through. Might this alleviate the pressure placed on it by cross currents? BTW – Are you a BP engineer and if not are any BP engineers taking stock of this discussion ?
"The reason there is no or low pressure in the non-pinched portion of the riser is because it’s open on the end, and exposed to the 5,000ft of head of seawater, which communicates through the fluid right back to the wellhead, if you cap the riser it’s no longer exposed to this pressure and it will try to equalize with whatever pressure is at the wellhead"
This is fine, your reasoning is correct. The first part is a bit shakey, and is untrue but the bold part is correct. But what if the wellhead pressure isn’t as high as you think?
You ARE NOT going to avoid Bernoulli’s equation and Q=V*A. Even with 18 5/8" pipe, it makes no difference on my calculations. The velocity is still slow. For this reason, pressure drop inside that pipe is essentially 0. The fluid is barely moving, maybe .1 m/s, that is 4 inch/sec. Don’t even worry about the kink, it makes no difference in the flow rate. Stepping on a hose in the middle makes no difference to the flow rate at the end, Bernoulli’s says so. If you step on a hose, you make the area smaller so the velocity becomes bigger to compensate. You don’t have a change in flow rate because you squeeze it.
The fact of the matter is, the velocity is slow right now. I dare you to calculate the velocity, doesn’t matter where you calculate in the pipe, because Q=V*A. If the velocity is so slow, the well is essentially already capped. So how is capping it going to increase the pressure and blow the riser to pieces. The only way you’re going to increase the pressure drastically is if you start shoveling dirt onto the ocean floor and increasing the wellhead pressure. I dare you, take some of your ideas to your university, go to the ME department, talk with a PhD, tell him your supposed wellhead pressure and have them calculate how much oil should be flowing out of your pipe. You’ll find that its probably well over 1mil gals/day.
You are essentially half right and half wrong. The pressure will increase when capped, only to the extent for which you had a pressure drop, but the flow is so slow right now, its essentially capped. It is barely flowing out. If it wasn’t equalized, the velocity would be much higher right now.
Answer this question. What induces flow? Energy minimization. The universe tends to minimize its energy. You surely know this from thermodynamics(I hope). Fluid flow takes place from high pressure to low pressure which is a pressure gradient. If the pressure gradient is larger, the flow will be larger. I guarantee you 210k gal/day doesn’t flow when you have a pressure of 10000psi inside your pipe flowing to 2200psi.
Have you thought about the the hydrostatic pressure of the oil?
This reduces what you actually see above the BOP, where we plan on capping it. Look a the picture.
http://www.yfrog.com/3d89725381p
Just because you cap the well doesn’t mean that hydrostatic pressure disappears. It still has a weight.
Again and again. With such a low flow rate, you people must understand, the well is already essentially capped by itself. There is very little pressure gradient otherwise our velocity would be much higher!!! Cap the pipe and put it to bed. You say the pipe can handle 600psi. Then I guess something like 10 Pa wouldn’t make a difference.
fbrad46
the friction of such a conduit on the oil would slow its ascent resulting in clumping and backup. Its not significantly less dense than water