Posted on
May 17, 2010 by
bp complaints
New Deepwater Horizon images:
ROV attempting to activate Deepwater Horizon Blowout Preventer

Image by uscgd8
100421-G-XXXXL-_003_-_Deepwater_Horizon_fire

Image by uscgd8
Deepwater Horizon Oil Spill – MODIS/Terra Detail (with interpretation), May 1, 2010
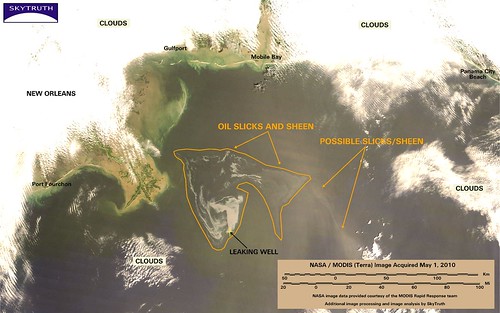
Image by SkyTruth
Tags: Activate, attempting, blowout, Deepwater, Horizon, preventer
Category
News
Trackback: trackback from your own site.
I can draw the workkable device on solidworks if you want because I’m designer
If the leak is at the middle of the pipe, device work with half of cylinder at the place of the cap
its already been stated, the riser pipe will not withstand the pressure build up if it is capped or plugged.
If there are pipelines in the area close enough to restrict anchoring near the site , assuming the oil flow can be contained, why does it have to be piped to the surface rather than routed thru existing pipelines???
Looks to me this is going to take more then two weeks from now or longer (3 months when relief well is drilled). That is the end of the Gulf Coast. I say: blast the well, close it immediately through force of explosion and then start looking at what has happened. BP and government have an obligation to the people of Louisiana, Alabama, Florida, Mississippi to stop the leaks as soon as possible
Horizon 37
Youve provided some pretty convincing arguments why applying a freezing jacket to the outside of the riser may not be effective, given the characteristics of well fluids. However, I still think there is a case to be made for making a hot tap in the vertical section of riser, if this could possibly be accomplished in the time scale. This connection could potentially be used in a number of way, (ie injection of dispersants, seawater, or extraction of crude oil)
I’m no expert, but learned that Subsea 7 trialed some new equipment for a grouted tee towards the end of last year, and details can be found on their website http://www.subsea7.com/technology.php (then click on subsea grouted tee). The company says that this system can accommondate some irregularities in the pipe section, but, of course, it would be necessary to clear any small bore pipes, cables and fittings from outside the riser.
If company decide to drill the soil, why they want to suck the oil in the soil if the other ROV continue to flow
That would be more efficient to use the second hole in the soil for injecting cement in
The grouted tee Marine Engineer is talking about looks promising maybe put 2 in the first one could handle the the oil and use the second one to maybe to plug the pipe . As the first tee should relieve some of the pressure downstream.
Hoodyz r us
I have no direct experience of pipe freezing. But as I understand it, the cooling is performed by coils of tube held within casings. Two or more casings are clamped around the surface of the pipe. Seawater is able to enter the casings, and freezes. The ice then provides a thermal transmission path between the coils and the pipe surface.
Hope that is helpful in anyu calculations.
Tee a reasonable consideration yet a 90degree turn would entail quite a angular force on the riser
Marine,
That is not the problem with blocking flow in the riser.
The wellhead pressure is probably around 3,000psi or higher right now. A brand new riser is only good for a little more than 500psi internal pressure and this riser is severely damaged, if you block the riser in one spot, it will just burst in another place upstream of the block, probably making the leak worse.
I have been thinking on the problem, and if it’s possible to remove a section of a choke or kill line at the isolation valve position between the blind rams and the pipe rams, there is a valve there between the ‘T’ in the line and the BOP body, if I remember correctly these are 3" ID valves, but being a 20kpsi stack they could well be 2", without the exact stack drawings for this stack I would not know for sure.
Once the ‘T’ section is removed a hot tap rig could be attached to the valve the valve opened by ROV and a fan tip abrasive jet cutter inserted to cut the drill pipe allowing it to drop down the well, at that point the stack bore would be clear and the blind rams could be cycled shut stopping the flow.
BP has announced they are building containment structures to place around the leaks, and pump the oil to the surface. See this link for a picture http://www.flickr.com/photos/uscgd8/4558317388/in/set-7215762394... This is essentially the containment scheme HowAbout2010 and I were discussing yesterday. It will be ready in 8-10 days, which seems like a long time, but is sure better than doing something that might further damage the BOP and increase the flow.
It has been stated above that "currents in this area are notoroious", and would interfere with any pipes to the surface. This simply is not the case. Surface currents are problematical now because of the winds, but that would not be a particular problem anyway. Currents in the spill area are usually fairly mild (less than 1.0 knot) except when the Loop Current impacts it. They can be 90 or 180 degrees apart at different levels, but riser engineers design for this every day. The Loop Current is about 180 n. mi. south of the site now, and rarely gets that far north. So, as one who has worked with these problems for many years, I don’t think currents will pose any particular problems for a riser from the containment structures to a surface collection barge. There are risers all over the northern Gulf contending with these (and stronger) currents every day.
This seems to be the most practical solution to this problem unless some intervention scheme that has no risk of damaging the BOP or pipes can be devised. If it can, then let’s try it, but continue with the containment structures.
The tees come in k or or y styles . thats what there literture says
Cutting the riser to accomodate the containment unit will change the dynamics irreversibly. Depending on the ram hydrallics that may facilitate the removal of the drill line and therefore the containment device would be superfluous as the rams could close.
A containment device constructed with an annular blow out valve would be more failsafe. A few ROVs could construct an improved mating surface for it before arrival
two 180deg opposed y joints with very low angular feeds into the surrounding network has its appeal. The inlets to the riser would need to be cut simultaneously by internal devices in the outflow pipes
Does anyone know if you can get to the choke lines? If you can, why not pump extremely high volumes of sea water and the friction will slow down the well considerably. Thoughts?
The high volume bullhead was one of the plans to kill the high volume gas cap wells years ago at Prudhoe Bay.
Does anyone know the diameter of the oil well and the temperature of the oil??
BOP is not moving,,,,,,,
Is it possible to hook-up
a vibrator,and try it?
@Phill.DeBill: nofx3378 spends all day schooling offshore drilling spill response wannabe posers as an educational specialist for BP. Life’s been tough for him lately. Give him peace.
Horizon37 seems very knowledgeable, but I wondering where the 600psi collapse rating of the riser comes from. I searched for spec online,but could not find it, and don’t have a copy of API16. However, typical deepwater marine riser is say 21" OD 19"ID in 80ksi yield. API5C would give a pressure rating 6000psi burst and 4400psi collapse. Would normally work to API6 for subsea pressure control, but in the cicrumstances API5C should do. Also when drilling an HP well may use mud as heavy as 16ppg giving circa 2,500psi differential on riser in 5000ft of water. I mention this as pressure rating of riser effects what may, or may not be feasible with regard to plugging of the riser.
I do generally agree trying to function the BOPs is probably still the best course of action short of a second well.
I think you guys are on the right track with the ice plug. It is definately just a temporarily fix but, anything to slow the flow will be benificial to all of us.
You can eliminate the idea of the use of a refridgeration device and nitrogen.
However you might be on track with the hot tap. Once the well head or BOP is tapped a methane / water mixture could be pumped VIA coiled tubing to create a hydratre seal.
I’m not scholastically educated – so how about you engineers do the math.
A marine riser is typically low pressure meaning it’s only deigned to withstand the hydrostatic pressure from the mud column. Therefore an ice plug on the riser will probably just burst the riser again. The steel in the BOP/LMRP is probably to thick to be able to cool it down sufficciently especially with the hot flow of oil coming out. If they could manage to get the riser off and the drill pipe inside cut somehow without increasing the flow sufficciently. The best thing would be to get back with some HP equipment on top with a couple of valves to shut off the flow. This could either be done on top of the LMRP or at the LMRP connector. The only risk as I’ve also mentioned above is that the flow might increase as you remove the riser and drill pipe as this seems to be choking the flow where the bends are.
Is there any form of oxidizer which can be injected into the oil stream which will then form a hypergolic reaction during the assent of the oil to the surface. In other words an oxidizer that would make its O2 available at a specific column of water pressure allowing the oil to reach the surface already on fire?
another viking
So what you’re saying is that the risers usually act only to direct the mud upwards so they are designed to be subject to the hydrostatic pressure of both mud and ocean, which counter balance each other allowing for 600psi difference before the riser collapses or bursts.
If we were to cap it or seal it, the hydrostatic pressure that is currently help restrict the flow/counteracting the internal pressure would no longer exist since it’s capped and the pressure inside the riser would build up to the well pressure which is supposedly around 3000psi.
My only issue with that is, currently the riser seems to be stable and hasn’t blown apart due to a tremendous pressure differential. If you say that the riser is good to around 600psi pressure differential, then the wellhead must be a below 2800psi or else the riser would have already blown apart. The way I look at it, you’ve got fluid flowing at .552039 m^3/min or .050295 m/sec inside that 19in diameter riser. The fluid is moving so slowly, that you basically neglect (rho*v^2)/2 in bernoulli’s equation because it is comparatively small with your other wellhead pressure term. So essentially, the pressure at the wellhead is equal to the pressure in the pipe. At 5000ft down, you’ve got like 2200psi of hydrostatic pressure. Assuming your 600psi bursting tolerance, the inside riser pressure should be below 2800psi or else it would have already failed. What I’m essentially saying its, the pressure differential between the exit of the pipe and the wellhead must be relatively small because the flow is moving at such a low velocity.
hyperphysics.phy-astr.gsu.edu/hbase/imgmec/bernoul.gif
Going over each term, knock out everything in the first half except P1. The velocity can be neglected because the well is enormous and you don’t have flow there. We set the reference height of the ocean floor to 0. Now since there is a difference in height because the pipe is on the ocean floor and the well is somewhere below the ocean floor so you’ve got more pressure added top of the well, but at the current moment something is acting like a pressure reducer in our system, otherwise our velocity should be much bigger, maybe the BOP has this effect, I do not know. This term should be counted ordinarily, but I’ll neglect it because somewhere in our system we have a pressure reduction that essentially knocks out most of the pressure difference due to height difference.
For the second half, you keep P2 and the (rho*V^2)/2, the height term can be knocked out since the pipe exit is on the ocean floor. With such a small velocity of .050294 m/s and a density of 850 kg/m^3, that is only like 1.075 Pa. So basically P1=P2, which makes sense because if the pressure of the wellhead was really high, the flow rate of that oil would be much greater. This all goes to prove that the pressure in the system must be low enough compared to the hydrostatic ocean pressure that the flow is very little and capping it wouldn’t be a problem. The oil is already moving slow enough that the pressure in the wellhead is equal to the pressure in the riser. If that wellhead had tremendous pressure, then the velocity would be much higher, and capping would be hard to do because of the pressure drop in the pipe due to velocity.
I believe this fully disproves any thought about the pressure being too high in the system. Now that isn’t to say things won’t change at some point due to something happening to increase system pressure. But at the current moment, capping it would be absolutely no issue. The riser directly above the BOP is in plenty good shape, no bending fatigue, to handle the slight pressure differential. I know some of the terminology regarding the pressure reduction isn’t all that clear, but the basic point is this, we don’t care where the pressure reduction is in this analysis, we just assume the pressure at the reducer is the pressure of the wellhead to make things simple. Sure the wellhead pressure is probably quite great, but that doesn’t matter when the regulator is introduced into the system. As long as that regulator stays in place, where ever it is, it should make things a lot easier to cap this riser.
To give you insight on my velocity calculation,
I took 210k gal/day, which becomes to .009200 m^3/sec
With a 19in ID pipe, that is .4826 m
The area of that is pi*(.2413)^2 which is .18292 m^2
Dividing the flow rate by the area, gives you velocity in m/s of .05029.
In the Bernoulli equation, you have kg/m^3 multiplied by (m/s)^2 which ends up giving you Pa or kg/m*s^2. So the unit analysis checks out.
It seems stopping the flow entirely would lead to a 1.075 Pa increase inside the riser. I’m pretty confident it can handle that.
Ok here comes a very stupid question but I’m gong to ask it anyway. I’m going for the there’s no such thing as a stupid question thing. If there is a steady supply of flammable oil flowing at high pressure is it possible to ignite the oil at its source on the sea floor? WIll it act something like a welders torch? You can light a torch and stick it underwater and it will not go out because it is getting a steady supply of gas. I know oxygen plays a pretty important role in this so will the oxygen in in H2O allow this to happen. I"m just about certain it will not. But, if oxygen is pumped down along with an ignition source and placed next to the oil coming out at high pressure will it ignite and stay lite like a torch and burn off a little of the oil before it reaches the surface? I know that at 5000′ and the pressure we are talking and the amount of oxygen required to do this sounds like crazy talk but I"m a little curious if this is even possible.
Remember the 11
Horizon 37 has experience of riser specification that I lack, however, there is a difference between the design specification of a riser, and its ultimate failure, particularly since the main stress on a drilling riser would most likely occur during deployment, when it is being lowered to the seafloor, and may subject to occilations from ocean currents.
Rough calculations would suggest that a thick wall (say 1-inch) pipe would withstand a greater pressure that 600 psi. But then the weak point would be the joints, and I’ve no way of estimating their likely strength. But again, these joints would suffer enormous stress as the riser is deployed, and I suspect that this would be a more significant issue for design than the pressure of containing mud, which is its function when in place.
Then the wells shut in pressure may be far greater than the 3000 figure. It would be interesting to know BP’s figure for this.
Anyway, there seems to be some consensus that provision of a tapping point at some point would open up a lot of options. Whether this is done by a hot tap operation on pipes associated with the BOP itself, or higher up on the riser, is a debating point. But a tapping point would open up a number of options including the injection of dispersants at source.
This would be a new line of attack on the problem, which could be run as a separate job, and would not interfere work of the emergency teams who are currently focused on more important issues of (a) trying to operate the BOP, (b) building a collection system for the existing leaks, and (c) drilling the relief well.
Jake 398
Burning the oil at source would seem to have some potential, though it could prove difficult to supply the oxygen and ignition source to ensure a steady burn. But one recent innovation may help.
The Carbon Capture project http://www.co2captureproject.org recently described a new process called ‘chemical looping combustion’ (CLC) which is being developed for for ‘oxy firing’ boilers. ‘Oxy firing’ involves providing pure oxygen to the burners, thus eliminating the need to pass nitrogen (80% of air) through the carbon capture plant.
The novel feature of CLC is that the oxygen is absorbed by a solid carrier, and thus the oxygen needed for combustion can be handled like any other solid. The system has apparently been trialed at 120 kw scale, so there must be some of this material available.
Some sort of phosporus flare could possibly be used for ignition.
downholeengineer,
The 80kpsi you are thinking of is the ASME connector flange designation. Normally the bottom joint (joint #1) of the riser is extra heavy wall 18-5/8" ID x 22" OD it is extra heavy here to withstand the forces of motion in the riser string, also since it attached directly to the LMRP ball joint it must also be thicker to withstand abrasion from the drill pipe, because as the riser bends back and forth at the ball joint the drill pipe is no longer centered in the hole, and may rub the inside of the riser, this can cause a key seat in the riser wall or eventually wear completely through it. however the rest of the riser string would be 18-5/8" ID x 21" OD, this gives a 1-1/8" wall.
A Marine drilling riser of this type VETCO HMF type H is rated at 3 million lbs pull, which is the preeminent factor in marine riser design, these tubes are not seamless pipe they are longitudinally welded, the riser on the Horizon is in 90ft sections, and has flotation collars of varying densities placed along the length of it to minimize the load both on the BOP stack and the pressure required on the tensioners which are only rated to 800kips, and to counteract bending dynamics. The Horizons riser weighed in the neighborhood of 4 million lbs without flotation
Riser pressure ratings are easily figured using ASME welded pressure vessel calculations. I stand corrected on my previous pressure, it was based on the pressure rating of the slip joint. The rating for this riser is 1468psi internal and 770psi collapse, still below what is needed to stop the well flow at 3,000psi.
A pretty much complete spec sheet on the Deepwater Horizon can be found here.
transoceanjobs.com/fw/main/Deepwater-Horizon-56C16.html?L…
http://www.flickr.com/photos/uscgd8/4563035602/in/photostream/
Looking at the picture above …. and reading the comments here about the strength of the riser pipe … and admitting I’m a complete lay person … I have to say this just doesn’t seem that hard ….
Use the HOT TAP method described above …
1. Build a HOT TAP collar that matches the riser pipe immediately above the BOP
a. Make it two halves that bolt around the riser pipe
b. Cut some grooves inside at either end for "o-rings" – maybe three sets each end so the seams can be offset …
c. Make it sufficient thickness to increase the strength of the riser pipe to withstand SOME of capped pressure
2. Include TWO "hot tap" "T’s"
a. One hot tap "T" just above the BOP riser pipe flange … this Hot Tap would have a valve that could be closed (a mini BOP) but that could also be opened enough to pass a cutting tool thru …
b. A second hot tap "T" large enough to include a ram large enough to allow blocking the riser pipe …. also include a similar valve as above – that can be opened for a cutting tool to pass thru
To use this HOT TAP:
1. BOLT around riser pipe – immediately above BOP riser pipe flange … butt to flange (or even machine the bottom end to fit over flange)
2. Once HOT tap is in place insert a drilling rig in the lower T then open valve in T to allow drill to drill a relief hole into the riser pipe inside the HOT TAP …. withdraw drill, close valve, remove drill rig from end of T and attach a new riser pipe to surface collection point
3. Once new pipe in place open valve again to allow oil to flow thru riser to surface collection
THIS COULD BE the entire short term "fix" … until they get a new relief well drilled etc … by creating a point to bleed and relieve pressure should minimize leaks in old riser pipe on sea floor …
HOWEVER … I believe the HOT TAP could be used further …
4. Once "bleed" is in place use the second/top HOT TAP "T" …
a. Attach larger bore drill rig to this bigger "T"
b. Open valve to allow drill to pass thru and cut thru the riser pipe and any other obstruction in riser pipe section inside HOT TAP section
c. Withdraw drill bit, close valve, remove drill rig, attach another "ram" type valve to the end of HOT TAP "T"
d. REOPEN valve and run RAM into the riser pipe portion of the HOT TAP to "cap" the flow into old riser pipe
e. Use the lower "bleed" "T" to manage pressure so as not to exceed riser pipe with HOT TAP reinforcement’s PSI rating
None of these connections, nor the "ram" blocking or "capping, would have to be completely/perfectly "oil tight" " … a small amount of oil bypassing and leaking would be a minimal problem compared to present
It would seem this HOT TAP "T" could be built in a couple days … and could be built to be installed by an ROV?
AGAIN – even if no capping effort was made .. but simply a HOT TAP …. that fed oil from riser pipe immediately above BOP to a new riser pipe to a surface collection method … it seems it would "capture" the vast majority of the oil that is currently leaking …
A quick, relatively simple, comparatively low tech method … could be simplified even more I’m sure … and it would seem could be built and on site in a few days?
Someone know the manufacturer of the BOP so that we can find the patent drawings ?
It’s cameron ?
http://www.coopercameron.com/content/products/product_detail.cfm...
Folks the long term solution is an engineering solution, right now in the short term we need a chemical solution. My suggestion of an oxidizer that will go hypergolic (in other words self combust) on ascent is the type of thing we need to look at. An oxidizer compound that is unstable at atmospheric pressure, but stable under high pressure is what we are looking for.
Once a chemical solution is on the site and functioning then we can take the risk of removing the riser and installing another BOP.
Also rather than skimming the surface oil, why not spray the oil with hydrogen peroxide and then imediately pull a silver screen trhough it to ignite it on the surface?
DO you know that hair is the best absorber of oil ?
USA people can give their hair and we can put in fillet bag for putting on the water
This avoid use of another chemical product
I have found
Model of the BOP
2 x Cameron Type TL 18¾in 15K double preventers; 1 x Cameron Type TL 18¾in 15K single preventer; 1 x Cameron DWHC 18¾in 15K wellhead connector
anatomy of the BOP
demopedia.democraticunderground.com/discuss/duboard.php?a…
With regards to making an x-ray of the shear valve. Depending on the current direction, it may help if it tends to hold the film against one side of the valve.
Perhaps a stack of multiple sheets of film each separated by a few inches could capture enough information to permit the computer folks to constuct a usable image even if things move a bit during the exposure.
I wonder what the diameter of the valve we are trying to Xray is. Perhaps 30 inches? I’ve heard stories of folks Xraying safes of similar size without the computer compensation.
Another suggested solution: Flattening the leaking pipe before the leak.
See http://www.inivention.nl/stop_oil_spill.pdf
Doesn’t seem like too much to ask from those robots, does it?
Well that magnetic sealing mechanism seems to be the way to go because it allows a crimp in the pipe due to plastic deformation. If you just smash it shut, it might crack. I don’t believe from my calculations above that crimping the pipe would be any issue due to the very small flow. The pressure drop inside that pipe is so small that it won’t make a difference.
http://www.google.com/patents?hl=en&lr=&vid=USPAT5188177...
Re: Relief Well.
What’s the status? One source says it’s already drilling, Another says it’s scheduled to be on location today.
Does it have to drill down to the producing zone? Don’t have a schematic of this well, but say there’s a 20" shoe 3000′ below mudline. Why can’t they intersect there and plug/divert flow? Wouldn’t take so long to drill.
is it possible to drill the pipe???
Recovery proposal:
Position a large tripod over each of the release areas. Tripod feet located on sea floor.
Between each of the legs of the tripod is some strong fast-to-acquire fabric, allowing the tripod to act like a funnel. Fabric would begin partway up the tripod, as necessary.
Top of tripod funnel is connected to tubing that directs oil to surface for recovery, with or without a pump.
All of the components of the above can be assembled and built quickly. Tripod should be stable enough to keep funnel over top of the leak points. All build materials are solid — differential pressure should pose no problem.
Status update 3rd of may:
BP is looking at installing a new BOP on top of the existing well, which could then be used to shut the well, BP executive Bob Fryar said.
Fryar normally heads BP offshore exploration operations in Angola.
Sometime in the next three days, BP will try to install a meter to gauge the pressure on the lower marine riser package (LMRP), which sits on top of the existing BOP, to see if it might be possible to install a new BOP on top.
If pressures are not too high, Fryar said crews could shear off the broken riser and LMRP unit and then "stab" or stack a second BOP unit on top of the original BOP.
The new BOP is already on board the Transocean drillship Discoverer Enterprise, which is believed to be on location.
Follow up on previous message:
Alternative idea; pls look at the BOP/LMRP photo available at:
oilstatesintl.com/_filelib/ImageGallery/Products_Services…
then have a look at the top Annular Blowout Preventor just under the riser joint. It shows a round flange with bolts, probably to keep the Annular Blowout Preventor connected to the LMRP structure. Remove half of the bolts present every other one in the circle.
What if you would shear off the riser/drill pipe just above the flexible joint.
Then lower a larger diameter pipe with a valve on top (open) and a flange connection at the bottom over the sheared off riser and leakage flow and place it onto the flange of the annular blowout preventor and connect by bolts every other around the circle.
Once the connection is firmly made, close the valve on top of the large diamater pipe to stop the flow.
I’m aware of the forces that this will imply on the flange, but I assume this top flange ring is quite heavy.
I wonder why BP considers to shear off the LMRP on top of the BOP stack before connecting a second BOP on top of the existing stack. It could be so that the LMRP is not strong enough to withhold the forces of the well when another BOP is placed on top.
I notice that the LMRP only contains annular BOPs which are designed to avoid leakage (rubber seal) instead of the shear rams in the BOP stack itself. This might be an explanation that the LMRP is not strong enough to withstand the forces of an valve/shear ram BOP installed on top of it,
Thanks for the update. I’m almost 100% sure the pressure isn’t too high to shear the old riser off the top of the BOP. I mean look at the velocity of the flow in the riser. It’s tiny. There is almost no pressure drop in the flow. If there was more pressure in the wellhead then we would have to be concerned. So basically what they plan on doing is capping it by means of bolting a cap(second BOP) on top of the current BOP. If the flow rate/pressure was really that high, the pressure drop in the riser would be much larger.
Think about it like this. If the wellhead pressure right now was like 3000psi, and the ocean’s hydrostatic pressure is like 2200psi. If there was little to no flow at all, due to kinks, similar to our current situation, the riser would have exploded already and we wouldn’t have anything left. If the riser can handle 600psi, then surely 800psi would blow it up.
If the pressure in the wellhead was at like 2300psi and there was little to no flow, it would ooze oil out slowly. The riser wouldn’t blow up or implode.
If the pressure in the wellhead was really high and the flow was really fast, it would cause a large pressure drop in the pipe. If the pressure inside the pipe got down to around 1600psi, then the whole thing would implode due to the large differential.
Obviously the pressure in the wellhead is above 2200psi or the flow would be reversed. So I think this covers the 3 scenarios that are possible. The pressure in that wellhead might be extremely high, but something else is reducing the pressure in our system, probably the BOP since its closed to whatever extent.
If you are going to advocate for the pressure being so high, then you’re going to have to prove to me why the flow is so low. And no blaming it on kinks in the line because if that were the case, the riser would have exploded already before the kink.
I think BP is doing the right thing with the second BOP, shearing that riser was the first step in my plan all along. Shear it above the BOP and then you have a nice small area to work with instead of 5000ft of riser like a snake on the ocean floor. If the second BOP won’t fit for some reason, at least you have a nice small area to use your funnel on.
what still surprises me is that BP wants to shear off the riser between the top of the BOP stack and the LMRP. This would mean that they also cut off the LMRP as well. They will install the 2nd BOP directly on top of the BOP stack without the LMRP in place.
Has this to do with the fact that the LMRP structure is not capable to withstand the reaction forces once the new BOP closes ? I learned from the specs of the circular BOPs inside the LMRP (white circular units on the photo) that these units will not take any vertical forces because they do not stop any flow but only seal against the riser pipes with rubber.
With the recent flooding that has taken place in the Mississippi Valley over the weekend the excellent visibility they have had to date at the well site on bottom is getting ready to be lost, the outflow from the river is probably going to cloud things up considerably for several weeks, unless there is a strong lateral or onshore current at play.
dt.burgess,
The Deepwater Development Driller III spudded the relief well yesterday 05-02-10, what has transpired so far, is the wellhead template and guidelines were positioned and set on bottom, they have now begun drilling a 36" hole to set a 30" conductor casing, this only takes a couple of days as they are usually only 2 -300ft deep, and what they are drilling is basically hard mud, the 30" with the wellhead support base will be run and cemented, then preparations to drill a 26" hole to a depth where the formation will support a 20" casing shoe, this has to be a fairly good formation because the 20" has the 18-5/8" wellhead and BOP guideposts, etc. on its top, it could vary between 800ft and 1800ft it just depends on where they find good formation, the 20" is then run and cemented. These operations all take place before BOPs and riser are run.
Re: Drilling to the producing horizon; yes they have to drill to there and cement it off, so that there is no change for the well to produce after the final cement plug is set, the wellhead cut off, and the well permanently abandoned. Also this is a directional well, they have to curve the relief well into the old well, and generally this arc is 1.5 to 2deg per 100ft, it needs to be this long to keep from sticking the drill string,and to give them room to steer the bit to intersect the old well bore. Since this is a cased hole they will have to hit the old well dead center so they can mill a window in the old casing to inject kill mud and cement. BP is estimating 90 days based on how long it took to drill the Macondo well, the relief well could take less time because they know the formations they are going to drill through, or it could take longer if they have problems. Drilling an oil or gas well is 30% science 70% art, so anything can, and usually does happen.
Ok lets go old school simple minded temporary fix. If there is no tap below the lowest choke point in the system. tap in to the pipe so an expanding/hardening product can be pumped into the line. perhaps below the shear. the largest chunks will need to be big enough to catch into the pipe and build up a restriction plugging the pipe. the oil flow will continue carrying the product to the plug until there is no more flow. then a permanent fix can be made. if the choke points and flow prove to be to much to plug this way, perhaps injecting liquid nitrogen into the line way up stream could cause a freeze block.
I would think the kink in the pipe should plug fairly easily. and continue filling until a no flow status is reached. Put a hair ball in it fellas, lol Good luck