Posted on
May 17, 2010 by
bp complaints
New Deepwater Horizon images:
ROV attempting to activate Deepwater Horizon Blowout Preventer

Image by uscgd8
100421-G-XXXXL-_003_-_Deepwater_Horizon_fire

Image by uscgd8
Deepwater Horizon Oil Spill – MODIS/Terra Detail (with interpretation), May 1, 2010
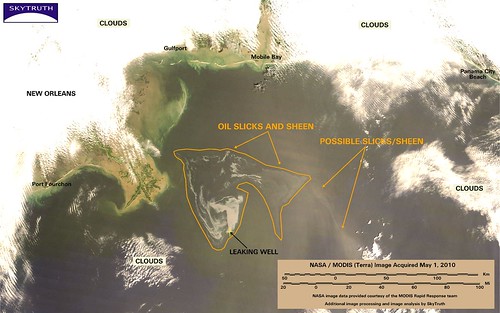
Image by SkyTruth
Tags: Activate, attempting, blowout, Deepwater, Horizon, preventer
Category
News
Trackback: trackback from your own site.
Greenpeace did it. to stop the proposed increase in off shore drilling. The charge was mistakenly set where it caused an unintended secondary explosion. resulting in much more damage than intended.
I would imagine the cause of the eventual sinking will be two fold, one of the bulk silos, or fuel tanks in the caissons exploded from heat, or some of the water tight doors to the caissons were left open during the evacuation, and water from the fire boats filled up the one of the pontoons, and the list of the rig went too far over center and it capsized. From the side scan sonar pic they have of the rig on bottom shows it laying on its side, so one side of the rig had more buoyancy than the other. Due to the depth, a distinct cause may be unknowable as any watertight compartments that were intact probably imploded on the way down and hull damage will be extensive.
Another cause could be the initial explosion caused a powerful enough shock wave that it damaged the thruster seals or sea cocks, and the rig just took on too much water to stay afloat.
I know we’re getting off topic, but this question has been nagging me. Shortly after the rig sank and the spill was identified, one "expert" said there would have been no spill had they simply let it burn. He said the rig sank due to the fire boats flooding it. I don’t buy this for a couple of reasons. First, I don’t believe the steel could withstand the continued heat exposure without ultimately failing. Second, it doesn’t seem that adding water to the platform would flood the caissons . . . unless they were already jeopardized . . . which would mean it would sink regardless. With the derrick rating plus the platform weight, this beast was engineered to support a LOT of weight. Is my logic flawed or was the expert just trying to get TV time?
Looks like they are thinking along the same lines as Hammer Mechanic… http://www.rigzone.com/news/article.asp?hpf=1&a_id=92872
In an odd twist, the possible fix would use the blowout preventer that was in place when the rig exploded, burned and sank. It may have failed April 20 when a sudden burst of high-pressure hydrocarbons apparently shot from the well and up to the Deepwater Horizon, triggering a fire and explosion that killed 11 workers. The new plan is for robot submarines to remove a control mechanism from the blowout preventer and reconfigure it. Then, hoses will be inserted into existing choke and kill lines on the device. Barges on the surface will first pump what Hayward calls "junk," or pieces of matting and rubber, into the well, followed by heavy drilling muds that should provide adequate pressure on the reservoir to close it.
dsw93,
Your logic is flawed LOL, just kidding.
Once the rig sank the oil was not coming up at a rate sufficient to support combustion.
For a fire to function you need 3 things fuel, oxidizer, and heat, if you remove any of the 3 fire cannot happen. In this case the fuel supply died off as the rig sank taking the fuel with it. And in order to burn on water oil has to be of sufficient thickness to insulate itself from the cold water, if it’s not it can’t maintain enough heat to sustain combustion. That is why the controlled burns they do work, they gather enough oil in one spot so the oil is in a thick enough layer to burn. The oil itself doesn’t actually burn it’s the vapors coming off of it, once all the volatiles are burned of from crude oil what’s left is basically hard tar or asphalt, often it just sinks. In this case even though there is a lot of oil coming up from the seabed it’s spread out over a large area by the time it surfaces from 5,000ft and the layer is fairly thin it most likely will not sustain combustion.
As far as fire boats sinking a rig, you bet! I have seen them sink ships, they put out a huge amount of water and you can see from the pics that there were 8 to 10 of them at a time hosing down the rig, and if any of the hatches, ventilation stacks and doors were open on the deck leading to the caissons they would eventually fill up with enough water to sink, and since power on the rig was shut down, there would be no automatic bilge pumps to pump it out. The fire boats hosed the rig down for 2 days straight before it sank.
Also you have to remember that when the rig sank taking the riser with it, it went down in a hurry, and oil takes quite a while to get to the surface from 5,000ft when traveling through water, it comes up at less than a 1/4 the speed of an air bubble. That’s why they first announced there was no flow, but the next day there was.
And by the time the rig sank the derrick was gone, so was most everything else on the deck.
Here is a good pic of the rig not too long before it sank.
images.rigzone.com/images/news/library/other/1/6703.jpg
If you notice the column sticking above the deck that looks like a candle with wax running down it? that wax is what’s left of a 75 ton deck crane. based on that I can say for pretty sure there were holes burned through the deck, and that gave entrance to even more water from the fire boats to get into the caissons.
Horizon37,
I completely agree with the reason the fire extinguished after the rig sank. That would have happened even if the flow was not choked. I also agree that a fire boat can sink a ship — which has an "open top" and a hull that collects water. But aren’t the caissons on a semi-sub sealed, as such preventing water from entering? Even if all of the mechanical, crew, and storage compartments held water, I cannot imagine that being a vastly heavier load than is normally experienced when the derrick is under full load. I guess what I am trying to say is the caissons seem to have been compromised at some point, and the rig was destined to sink as soon as that occurred. The use of fire boats only accelerated the process. Maybe I am just missing some fundamental understanding of the semi-sub’s construction.
Lisa,
As said before company execs sometimes shoot their mouths of before they have a full set of facts. In order to do a top down kill they have to isolate the well, they have not been able to do so to date, because there is junk in the BOPs preventing them from closing and this leaves the riser pinching off the flow from the well, the riser is severely damaged it was not designed to hold well pressures even when new. best estimates are that the wellhead pressure is around 3,000psi brand new riser is good for 1,400.
Just bashing into the riser with and ROV below the kink could cause it to rupture then we would end up with 60,000bbl/day mess instead of a 5,000bbl/day one.
IF and that is a BIG IF they can get the ROVs to hook up a control umbilical to the BOPs they may get a pressure read out from what pressure is in the BOPs. The umbilical connectors were not designed to be ROV friendly, they are a bugger to install on the surface with 2 people and air hoists, and they may have to fabricate some special tools just to attempt it. BOP Umbilicals are about 8" in diameter and about as stiff as a 2×4 and very heavy.
dsw93,
Actually ships decks are far more water tight than rigs, they are a way closer to the water than a semi’s top deck. On a semi there are at least 2 mushroom or goose-neck type ventilators on the top decks for each caisson, there will also be a stair or ladder well on each one, as well as a cargo hatch large enough to accommodate the biggest piece of equipment that would be installed in one. Below decks in most modern semis there is an elevator in each caisson accessed through the tween decks, below the top deck. If you look at the pic of the DH it’s bottom under the top deck is enclosed, this enclosed area has mud pumps, mud pits, sack storage, cementing unit, bulk storage, machine shops, work shops, warehouses for spare parts, offices, you name it, there is no wasted space on a rig. If the upper deck burned through which it probably did, the firewater the boats put on deck would have run into these holes, filling up the empty space the sponsons and caissons. With the rig at drilling draft the ballast tanks in the sponsons would be pretty much full already.
The initial explosion was from gas, so it would have just been a very large boom with accompanying shock wave, this shock wave would have traveled through the seawater and damaged ballast valves, sea chests, thruster seals, any number of entry points for seawater to get in to the sponsons. These rigs are no different from any other floating vessel, if you fill them up with water they sink.
Actually I think company execs can shoot their mouths off even after they have a full set of facts as well. After all, the article is dated May 7th. It seems as though he would have all of the facts by now. BTW, here is a link to an actual picture of the bent riser. It is the first I have seen.
http://www.nola.com/news/gulf-oil-spill/index.ssf/2010/05/feds_t...
Lisa,
The original BP article appeared in the Houston Chronicle in the evening edition of the 5th, Rigzone put in their morning opener on the 6th, looks like nola did it today. And I certainly hope no one takes the nola article seriously, their graphic is so wrong it would be laughable if this wasn’t so direly serious.
If you know anyone over at that rag or the Times Picayune, you better tell them to pull that whole story before they get their caboose sued off. The BOP layout is WAY wrong, the drilling procedure is wrong, the cementing procedure is wrong and the overall article is totally misinformed.
But thanks for the pic of the riser, this is first side view I’ve seen with the LMRP and gimbal shown.
Horizon, I should have figured as much. I wish that someone with knowledge would actually inform us and write articles for us. I wish that we could see more actual photographs or diagrams that are true and drawn to scale. I am very curious as to the actual state of things. Over the past few days I have read every single post on here in order to gain more true understanding of the situation. There is no good information in any of the news outlets. And as for the Times Picayune being a rag, yes, I agree with that too. I haven’t given them a dime of advertising revenue in years for that same reason.
I can not figure out how to send the info from Morgan Stanley. I recieved it on a pdf. It has 2 eyewitnesses accounts of what happened in their words . It was one hell of an explosion. One guy claims it blew the generators off the platform .
http://www.glgroup.com/News/Little-by-little-facts-emerge-regard...
Here’s a link to one interpretation based on information received. Take it for what it’s worth.
Someone screwed up and allowed someone to talk them into a big mistake if the analysis posted by M Lynch is close to the truth. And if this was all true from eye witnesses then this accident wholly and completely belongs to BP. Transocean’s insurance should be pursuing BP for the losses.
hdbob, dsw93
Let me guess these 2 guys are remaining anonymous?
If one of them said it blew the generators off the rig, that pretty much chunks his story out the window. The generators are below decks, they are welded to massive skids, They are same generator sets they use on train locomotives, or light freighter ships, they’re HUGE, if the explosion was big enough to blow the gen sets off the rig there would have been nothing left of the back end of the rig. Either he’s not from the rig, or he’s a galley hand or steward that wouldn’t know squat about the rig except where his bunk, the TV room and the galley are. As far as the rigs gen sets racing away on gas, can’t happen they have gas detectors on the air intakes to the motor room, at the first trace of gas they automatically shut the engines down, and when they shut down for a gas alarm they automatically drop flappers on the intakes of the engines.
The only folks that really know what happened are not talking for legal reasons, or can’t because they are with God now.
I agree Im just reporting what i got. Im not going to theorize on this I dont know the facts . I just work on equipment all day. So I will keep my bias out there is enough of that all ready.
txgho1911,
You can’t put the blame solely on BP, because the Transocean tool pusher should have told them to go piss up a rope and called his boss in town and explained the situation. Then shut the rig down until he got permission from Transocean brass to go ahead. Granted you don’t want to piss off a customer that has your rig contracted for 3 years at a rate that will have it paid off in that time. But if they did what is being rumored they did it guaranteed a blow out or at the minimum a casing collapse. In either case they would have lost the hole.
Some searching has produced more "fly on the wall" commentary.
blog.iongeo.com/?p=1961
http://www.ogfj.com/index/article-display/2323778238/articles/oi...
http://www.sott.net/articles/show/207968-Expert-Views-on-the-Dee...
Very detailed description of the riser.
http://www.drillingahead.com/forum/topics/transocean-deepwater-h...
gcaptain.com/forum/offshore/
Horizon I agree and and there is so much disbelief the entire floor crew would not protest such a spectacular error.
Some of the commentary I linked mentions Halliburton did not set plugs and another one says they did.
I am diving into the forums monitoring this topic as many more insiders are present there.
What ever happened to the installation (as quoted by a Mr. Fryer a couple of days ago) of a pressure gauge to the BOP. Is it that hard for a ROV to do?
Horizon,
Gas hydrates prevented cofferdams from working, so now it looks like on to the next option…Topkill.
Even if they were able to connect to the choke/kill lines via ROV’s and pump in rubber and golf balls without bumping into or touching the risers, couldn’t the riser still be destroyed if those golf balls make it past the BOP’s? I mean BP does not seem to know the size of the obstruction in the BOP’s, so it would seem as though the well could conceivably "produce" golf balls sending them into the fragile riser possibly at high velocity. This seems dangerous and desperate to me, possibly something that should be tried closer to the point at which relief wells are finished. Why risk removing obstructions to flow unless the flow rate is already much greater than the 5,000 bbl/day figure they are using?
Horizon 37
Your posts are very clear and sensible. I had (retired) 30+ years in the oil business but not as a driller. Reservoir Engineer. Can you clarify one point for me. You have speculated that the BOP failed to fully close because of some obstruction, probably a drill collar, that the ram shears could not cut. Sounds feasible, except I understand they were coming out of the hole after setting and cementing the production liner. If so why would they have drill collars on the string? Also, it has been said they were circulating sea water in the riser to displace the mud – wouldn’t the drill stem be in the riser and out of the BOP for that?
Appreciate your explanation.
4:15 p.m. | Updated Officials for BP on Saturday encountered a significant setback in their efforts to attach a containment dome over a leaking well on the seabed of the Gulf of Mexico, forcing them to move the dome aside while they evaluate find another method to cap the crude oil flowing into the Gulf since April 20.
Officials discovered that gas hydrates, ice-like crystals lighter than water, had built up inside the 100-ton metal container. The hydrates tried to make the dome buoyant, and they also plugged up the top of the dome, preventing it from being effective.
“I wouldn’t say it has failed yet,” Doug Suttles, BP’s chief operating officer, said at a news conference in Robert, La., “what we attempted to do last night hasn’t worked.”
As a consequence, they had to lift the dome off the well and placed it on the seabed.
The choke and kill lines are out here is a side view, as you can see they are kinked shut. And the only other way into the stack is to remove the LMRP, which they can’t do. Here is a link to the side view of the kinked and collapsed riser twitpic.com/1m8f4c as you can see it has the gimbal joint pulled over and there is not enough room to put on a saddle tap, even if one could be made to fit the egged riser.
Sharba1 it is most likely a tool joint or something else at the shears, from all accounts, they had the drill pipe at 8,000ft and were circulating to sea water, if this is a fact? someone needs to go to jail for the murder of 11 fine people. And for the largest oil spill in US waters since WWII.
Hopefully they can rig up a larger methanol line, or pull up the cofferdam and weld another layer over the top, so they can fill the layer with hot water.
Does anyone know if they got oil to the surface, or did it plug off right away?
Would a heat coil or circular coil of pipe inside the top with hot water circulated through this liquefy the ice long enough to rise into the riser? They have the water jacket there for this purpose.
a few riser pipes in a matrice through the cofferdam with sea water pumped down from the surface may help. Like the system used in heating diesel. The matrice being steel and the cofferdam being steel would minimise structural weakness from the pipes insertion.
multiple small feeder pipes with exterior foam insulation prior to entering cofferdam would increase surface area exposed. That would keep the heat coming from low down to up whereas a layer on top would not be as effective due to heats rise
txgho1911 just saw your post after i had posted. Enough surface area of piping at a warmer temp would make a difference, dont know what area /temp thatd be
a compressor running on top of the cofferdam that compressed ammonia into the coils so its heated (ie like a refridgerator in reverse) would eliminate the need to transmit more seawater down
that containment dome worked out great didn’t it
these guys are looking more and more like amateurs every day
fabric containment tube certainly couldn’t work any less effectively
use the same material and fabrication process used on sewage lagoon liners
might as well since the current approach is looking like sh… right now
Find it hard to believe that they would drill without even a clue as to how pump the oil to the surface. What a bunch of children. This is directed to management and engineers not to the people working on the rig.
Horizon, if you would shoot my idea down also. I was thinking a sort of impromptu BOP. A hydraulically driven jacket that would clamp onto the outer casing, shaped charges to blow most of the bad piping off, then use a diamond saw to cut the outer casing off, jack the saw up some, cut the well off clean (saw would probably need to be able to travel in a circle around the pipe to cut without getting in flow) then have an arm to swing a valve over the well and clamp it on?
I know this is not something you could find at a hardware store, but seems like one could be built faster than a relief well can be drilled.
Good mornin all, how have we been doing? I heard of the problems they have been having. Does anyone know if they have been working on plugging the leak from in the BOP while all this was going on? I have been away fishing and have not been keeping up.
hammer you been fishing, are living on the gulf and getting in your emergency season before the slick is to thick
No I live in Oregon now, I usually fish Hells canyon. I have been hoping to get down there in the near future for some fishing. I have family in Estero FL. so lets get this oil stopped Please lol. I`ll go down and plug it for them if they want.
Looks like we need to redesign the cap. Not make a new one. Improvise with what you got. We really dont have time to hand wring do we?
From listening to this discussion, something seems strange in the design of the shear rams in BOP’s in general. In the normal course of drilling, it is necessary to put things through the BOP that the shear ram’s can’t shear.
This seems contrary to the purpose having the shear rams as the ultimate failsafe.
What goes down the hole seems mostly shearable with an occasional unshearable hard part like a joint, hanger, or bit. Perhaps if there were 2 shear rams separated by some vertical distance and a rule that no hard part can ever strattle both shears at the same time.
Or maybe they already do this and I just don’t have a clear enough idea of the BOP?
now your trying to use common sense. I don’t think they are ready to do that yet. It could cost a few thousand more dollars.
And to any and all you ladies out there.
HAPPY MOTHERS DAY
I hear Al Gore’s boat was spotted in the area just before the trouble.
Right now we have a problem and need to think about how to get around it . dont think im not agreeing just tring to get back on track . How about heating the cap with resistance heat . The pressure shouldnt effect that should it ?
is it 60F(16C) enough?
The problem with heating the cap is it will cause the gas hydrate to change states. When this occurs you will have very flammable Methane reaching the surface. This is what I believe caused the fire in the first place.
This forum has been a fascinating read, a real education to one not very familiar with the technology. Now a couple of questions:
1. If a tool joint has jambed up the BOP, can a BOP stack be configured in such a way such that a tool joint will not obstruct all the rams? More spacing between rams? Redundant shear rams spaced so that one shear will always be clear of a tool joint? Annulars top and bottom?
2. Can someone here describe the procedure/process of installing casing in the hole? Does it line the entire hole, or only the unstable geology above the bedrock? Is it all the same diameter? Is it driven (hammered) down the hole? How to get one section past another? How to get a drill bit whose diameter is greater than the casing, up/down thru it? I’ve searched the web and can’t find an explanation.
From what I’ve been reading here resevoir pressures are expected to be very high, upwards of 100,000 psi, with potential flow rates greater than 60,000 bbl/day. Based on this it seems quite impossible for BP to do anything to this well, other than contain the flow, before the refief wells are completed and relieve the pressure.
Once this is accomplished, how is the BOP going to be removed from the well head with a bunch of junk pipe thru it and down the hole. With the riser cut away will the BOP be pulled up dragging the string of junk behind it?
Do we have any good pictures of the leak at the kink? something that shows the pipe in the area of the leak and kink?
I don’t believe the pressures are near that high, but does anyone know yet about how much pressure there is? that is the crucial piece of info we need right now.
Optimusnine
When the methane hydrate goes up the pipe it’s going to change state anyway as pressure is reduced and/or temperature increases, will it not? Somewhere in the process they will have to deal with it. Maybe vent/flare it at the top of the pipe prior to the separator? How could they keep it in a managable hydrate state? Stability has been one of the big problems with recovering methane hydrate as an energy source, it’s stability issues.
I`m looking at ways to stop the flow of oil from the well, not recovery. if we can stop the flow there will be no more recovery except for the oil already out.
Not sure where I read about that 100K pressure, can’t find it on here. But hydrostatic pressure, strictly speaking, thru the water column and bown the hole would be a little over 10K psi. To overcome this hydrostatic pressure an blow all the mud out of the hole to above the derrick I would expect resevouir pressure to be significant.
One of the other people said 3000 psi and another said up to 10,000 psi . The hydrate is going to change states they said bp was going to vent /flare it on the recovery. Did they try to hook up the umbilical cord and hydralic lines up to the bop?