Posted on
May 17, 2010 by
bp complaints
New Deepwater Horizon images:
ROV attempting to activate Deepwater Horizon Blowout Preventer

Image by uscgd8
100421-G-XXXXL-_003_-_Deepwater_Horizon_fire

Image by uscgd8
Deepwater Horizon Oil Spill – MODIS/Terra Detail (with interpretation), May 1, 2010
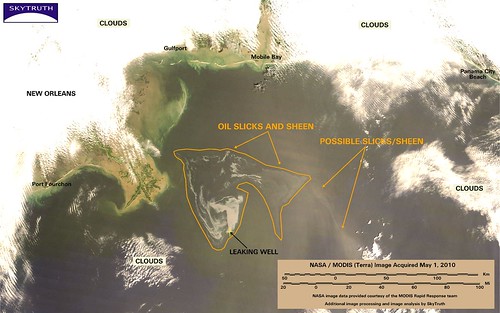
Image by SkyTruth
Tags: Activate, attempting, blowout, Deepwater, Horizon, preventer
Category
News
Trackback: trackback from your own site.
This is a fantastic photo. Thanks to USCG for sharing it with us. One question, though: since, as of Monday, April 26 at least, attempts to activate the BOP don’t seem to have worked, i.e. the oil is apparently still flowing from at least two points along the drill pipe, why not try to put a cap on those point sources, especially the one I’ve seen in photos- the end of an elbow joint-type pipe with oil spewing out from the end? Can one of the ROVs down there not not perform that kind of operation, using it’s robotic arm? Are you trying to do this? If not, why not?
Sincerely,
Gerald Graham, Ph. D.
On Scene Commander for Oil Spill Response
Gerry, Dispite posing as an authority on offshore drilling spill response you obviously know little about drilling operations themselves… that "elbow joint type pipe" you see is actually drill pipe which in NO WAY uses elbow joints. I’m guessing that is some Vam-Top connection which requires at least 15-20 thousand pounds of makeup torqe to even get a TIW valve on the end of it. This is far beyond the capabilities of ROVs.
Stick to the surface and shoreline issues with your comments where you belong.
Can the ROV be fitted with a hydrolic crimping tool that could crimp the riser one or more times to restict the flow rate??
@ nofx3378: Why so negative. It was a simple question!
Is the date/timestamp correct on this image? It indicates the photo was taken on April 22 at 01:08:54, but the rig didn’t sink until 10:00 on that date.
Re: Associated Press
I am not an expert on that particular ROV, but many ROVs have a "bottom time" stamp. It may not be the traditional time ( i.e.12:30PM/AM). This may say that the ROV has been in the water for 1 hour and 8 minutes….or someone may have not set the time correctly, after all these ARE divers… Clocks can’t be diver proof either…
Re: date/time stamp
Would be reasonable to expect that they might have been trying to activate the Blowout Preventer to try to extinguish the fire that had been raging since 4/20?
The lack of knowledge here is surprising. There is a low pressure wellhead here on top of a 36" conductor, and an 18-3/4" wellhead inside that with 20" or 22" casing below that and more casing strings down to the production casing which is probably a 7" liner string. On top of the 18-3/4" wellhead is the BOP stack connected to the wellhead with a hydraulic connecter, and on top of the BOP stack is the LMRP which connects the BOP stack to the Drilling Riser which is 21-1/4" pipe back up to the rig and diverter, the 6-5/8" drill pipe is inside all that. All of the drill pipe and riser went into compression and colapsed and buckled when the rig sank. The BOP stack should have gone to fail safe closed when they lost control signals and hydraulic pressure, but there may have been something inside the BOP stack, like a tool joint or liner hanger running tool that prevented the BOP shear rams from closing. There best bet now is to try and close the two annular preventers on the stack and LMRP
to temorarly shut the well in while they drill a relief well.
What the ROV is attempting to perform is to hydraulically stroke (via high pressure) the blind/shear rams with a HOT STAB. This hot stab is connected to the light blue hose and a pump that is on board the ROV. In order to stroke the rams (think of this as a huge piston connected to a sharp cutting gate) the opposite side must be VENTED to allow the displaced volume to flow. This could be one possible reason why the ram can not move. The other possibility mentioned above by rigdog is that there is a large cross section tubular in the hole that exceeds the cutting capabilities of the ram. A drill pipe should be no problem of getting sheared off, but it could be another wellhead component such as a casing hanger that was blown out of the 18-3/4" wellhead and is sitting at the same elevation as the gate.
Clossing the annular preventers is the next best thing to attempt, but some LMRPS do not have a hot stab provision for the ROV to intervene as shown on the photo.
ROV can put a plug in the pipe where the oil is come out with a thru tubing tool with a 1/4 inch line go back up to the boat and one the tool in the pipe you can set it and cut off the oil.
there is obviously considerable conjecture, ignorance and knowledge, as I read through the comments…people are interested and want to know is what has happened just before the well was lost. why can’t BP and Transocean come to the party and tell people what operations were underway, at the time the well blew out, to the best of their knowledge. It is as if it is some darned big secret…tell us, all people want is to know. We are all genuinely interested. Maybe we can all learn something…imagine that!..it is not as though the oil industry is viewed by the America public in a positive light…BP and Transocean might help by being forthcoming with facts..it is a very tragic event…
They said the well had been drilled to the full depth (18,000 ft) and they were in the process of cementing the last casing section.
cliffbourgeois.newsvine.com/_news/2010/04/23/4196590-deep…
See the above link for a very good description of the process & likely point of failure.
subsea1engineer,
From what little I can gather the well had been completed and they were preparing to temp abandon the well, there would not have been liner gear in the BOP Stack, Just a wild guess but they were pulling the drill string, and swabbed in the well, or circulated up an oil slug from a previous drill stem test. It could have been any of hundreds of things that cause the initial fire.hopefully they can recover the rigs computer logs and see exactly what was happening at the time.
The fire probably damaged the surface controls for the BOP stack, or rendered them inaccessible to the crew, and when the rig finally sank the riser broke off and damaged the stack control lines, and the stacks on-board emergency accumulators lost all of their pressure to close the shear rams or blind rams, probably all rams, depends on how the stack was programmed to respond. There is also on these stacks a battery operated sonar activated system to close the rams, evidently it failed or was damaged. And I doubt if the ROV has enough power to operate the hand wheels on the rams either. It would be nice if someone had gotten some footage of the area under the moonpool to see if the riser was still hanging after the initial fire, if its compensator wires had burned through the riser would have dropped before the rig sank, taking the drill string with it. this drill string is probably 4-1/2" as 6-5/8" as stated earlier would not fit inside a 9-5/8 casing the tool joints are to big.
As to the time stamp it is in all probability the ROV mission elapsed time time.
Gerry,
That bent piece of pipe is a 22" riser it has a wall thickness of around 1-1/4" which means it’s 24-1/2" OD, the reason it’s bent like that is because the rig dropped it and it has drill pipe inside.
With the drill pipe bent over at that angle, that annular BOP will not seal and in all likelihood the the drill pipe is curved or kinked in the BOP body, and the rams will not function if the pipe is too far off center, the shear rams may work as they have a "V" shaped notch in them, but they don’t have seals to stop the flow. And even if they shear off the drill pipe, without any way to remove it from above the shear rams, the BOPs other rams can’t function. This scenario is a subsea engineers nightmare. because there is no way to fix this with ROVs, they will have to position a rig over the well to cut and lift away the junk. And a relief well will have to be done and the well killed and cemented off, before they will attempt anything like that. It is going to be one HUGE mess.
Horizon37,
Yes, you are correct, the well was being prepared for temporary abandonment. At the time of the explosion, the drilling mud in the riser was being evacuated and off loaded to a container vessel and was replaced with seawater. This is effect was a "loss" of a critical barrier. However, and I must say SUPPOSEDLY there were still two barriers left downhole, the cement shoe plug and and packer somewhere below the casing hanger. There was still another piece of equipment called a lock-down sleeve that lands above the casing hanger that was not yet ran. This in effect locks the casing hanger to the wellhead and provides a seal bore for the tree stab. There are many unproven rumors circulating about that maybe some corners were cut and the cement job was not allowed adequate time to cure. None of this can be confirmed until the well is killed and the stack is removed.
O.K you guys really know your stuff so could you tell me if the following is possible. Can another (new) BOP be put next to or below the damaged BOP. Can they be connected by the ROV or using another method. Can the flow then be redirected through the old BOP and then through the new BOP (the new BOP is left open so the flow continues). Cap the damaged drill pipe or cut and seal the pipe at some point in the pipeline. Then trigger the new BOP.
I am assuming that BP is concerned that the only thing keeping the flow from getting worse is the kinks in the drilling riser and drill pipe. They have experience in retriving subsea manifolds and wellheads but this was only done under controlled conditions. Adding a BOP below the exisitng one is not possible without killing the well by filling it with a fluid that exerts a static head greater than the force of the reservoir pressure. Can’t do that with the current riser attached and the BOP non functional.
Subsea Engineers description of issues would appear to me to be fairly accurate. If you are really intersted in operations of a Subsea BOP hydril has a whole catelog (Blowout Preventers CATALOG M-9402 D) online at http://www.hydril.com. One thing I would note is that catelog states that for the 20,000 psi rated BOP (which given the HPHT nature of the lower tertiary most likely was the horizons being targeted) it does not use well pressure to help hold in the rams but must rely on hydralics. It takes avbout 12 gallons of 3000 psi fluid to actuate the rams to a closed position. Normally they have that sufficient volme in the subsea accumulators. However with the rig and surface HPU compromised it may not be possible to know if there is a leak in the circuit that has bleed the system down. I have worked more with the subsea production trees which are designed for installation subsea of what is called flying leads to hook these sort of things up. I think the drilling BOPS are lowered using the riser and the drill rig so the connections may not be ROV accessible. The industry may need to rethink this for furture designs to allow for a plug in override of the hydraulics and the control pod.
Just some thoughts. It would be nice for BP and Transocean to open up and allow more input from the industry. However, they tend to try to keep most of this information pretty close to the vest. They know they are going to be sued by everyone unde the sun so they are in damage control mode. Our societies litigous approach to these sort of incidents mandates that they do.
The problem is that there is currently no suitable locking/sealing profile available for the "new BOP" to attach. If EITHER the BOP or LMRP connector could be unlocked and this huge mass picked up and removed from vetically ABOVE the wellhead, the new equipment could be lowered down. landed and locked by ROV. The main problem with that is both said connectors operate hydraulically from a subsea unit called a control pod. Apparently, no secondary means was designed for an ROV to intervene the primary hydraulic circuit routed from the control pod.
The riser pipe can and will eventually be cut in sections by a specialized ROV after the flow is halted, but any attempt at the present time to attach a closure device on the end is futile without a locking profile and a "clean" and concentric sealing profile as mentioned above.
Could somebody please explain why they don’t position some type of products tanker with pumping capability directly over the spill site, lower long suction hose(s) over leaks with the ROV and suction oil and water at source of leaks up to the tanker. Thank you.
Not being a offshore drilling person I wonder if a heavy cap can be fabricated and lowered over the BOP. DP Derrick barges can lift loads heavier than 3000 tons. If the pipe could be cut above the BOP and moved away just before the cap was lowered this would provide a seal to the ocean floor. If cutting the pipe is not possible then a crane could attach to the pipe moving it up and down until it severs and then it could be moved away from the BOP. Sounds simple but I know it’s not at 5000 feet. However the most simple things usually have a better chance of working. If something is not done in short order, the entire coastal Gulf area will be covered in oil.
I have an idea to stop the flow of oil into the gulf coast. My idea revolves around the use of device that anchors itself inside the diameter of the pipe using three legs that expand at an angle against the flow in the pipe ID (like an anchoring devices used in old bicycles head stems). Then, just above the anchoring device, a mechanical device or hydraulic device expands a thick rubber bladder to plug the orifice. This device would be similar to a angioplasty used to remove plaque from arteries.
I think the only possibility to shut off the flow is to disconnect the LMRP, try to get the junk above the shear rams out and come down with a different LMRP (I’m sure Cameron must have some available) with a valve on top. Then once the LMRP is landed, shut off the valve on top or possibly close the annulars (if unable to remove all the junk above). I realize it is quite risky as we don’t know exactly what, where, and how much of the maximum potential flow that is being choked. But if one knew the maximum potential production profile for the well (which I assume BP must know quite well), this risk could be estimated. Besides they must be able to see how far the shear rams are closed based on the ram position indicators, and I would expect that some of the flow must be choked down there and that the junk (e. g. drill pipe) is impaired/squeezed.
Alternatively, if they have side access below the lowermost ram (which is required in other parts of the world) they could possibly try to hook up with a kill line and start pumping. Chances are that it won’t doo much good and that it only will come out with the oil, but it shouldn’t do much harm either and it is probably less risky than the first alternative. But I don’t know if they have access below the lowermost ram as certain API codes does not allow for this.
It would be great for people to submit their ideas to stop the oil from flowing. Brainstorming can spark an idea that engineers can run with. Apply the engineering rule KISS (keep it simple stupid) and maybe a quicker solution can be put into play. The offshore industry has the ability to fabricate steel rapidly, especially if fab yards work together on a common project. We are a great nation with smart people. Surely a solution to shutting off the flow of oil can be found if we begin to think outside the box. The three legged plug is an interesting idea, but I’m not sure it can be lowered into the pipe due to the PSI and volume of oil flowing from the break. That’s why I suggested a heavy steel cap to cover the BOP ands use the ocean floor as a means to seal or as a minimum limit the flow of oil. How about more ideas from engineers and mechanically inclined people.
My Suggestion for arresting escape of oil to the environment:
Lower approximately 12 Ft Diameter X 100 Ft long cylinder over each leak source.
Make cutouts if and as appropriate at the lower end of cylinders.
Lower appropriate number of suction hoses or submersible pumps into the upper ends of the cylinders.
Pump the oil to surface collectors at a rate sufficient to prevent oil from escaping out of either the top or the bottom of the cylinders.
Here’s another idea. Fabricate a heavy (weight) clamp that has a larger diameter than the existing pipe . The clamp must be able to reduce it’s ID smaller than the OD of the existing pipe. The upper section of the clamp must also have a larger diameter than the pipe to accomodate a shut off mechanism. Cut the pipe above the riser and lower the heavy clamp via a DP derrick barge. The weight of the clamp must be sufficient to prevent the oil pressure from blowing the clamp away from the leaking pipe or the clamp may be attached to the ocean floor and positioned over the pipe via pulley arrangements and the crane working in unison. Actuate the clamping device so it is attached to the pipe with enought force to hold the pressure of the oil. Once the clamp is attached actuate the shut off mechanism.
Lowering durable cylinders (able to withstand extreme underwater pressure) to just above the leaks seems to be the way to go. Remote underwater pumping carries the least risk of contacting and accidentally rupturing the riser/pipe and thereby making an already bad situation worse. This is a temporary solution to absorb most of discharge until a relief well is drilled or some other solution is found.
The cylinders I proposed would be open ended at each end with no concern about extreme underwater pressure since the interior pressure and external pressures would be equal. The cylinders would serve only as a barrier to prevent the oil from mixing with seawater outside the cylinders before being pumped to containers at the surface. A fair amount of sea water would also be pumped to the surface, but at that stage separation of the oil and that water would be relatively easy to achieve.
Guys are you serious, read the news, BP has been in the process of constructing just such contaiers for days now. They will lower these and pump the oil back to waiting barges, it will take another 3 weeks before these are deployed, until then containment at the surface seems the only option.
How quick can pipe be connected from the surface to the three leaks? Drill pipe, pipelay barge, reel barge or any combination?? If this can be done in a reasonable time frame then 3 pipes with a large funnels attached to the end can be lowered directly over the leaking areas and subsea tensioned to a DP rig above where the pipe would be connected to a pump(s) ( Possibly a borrowed booster pump from loop in Fourcheon). Tankers could be standing by for loading and they could then offload at loop and return to the rig. At this point money is not an issue as the cost of cleanup and damage far outweighs the cost of any solution.
3 weeks. Considering this is can and may be the worst environmental disaster in US history this time frame is unacceptable. If it would have taken 3 weeks to build a Liberty ship during WWII we may all be speaking german today. Surely a consolidated effort is required by all industries that support offshore construction and ship building. No stone should be left unturned and manufacturing facilities should be coordinatiing this effort to reduce this time frame. Strong leadership is what is required to accomplish this and believe me this makes all the difference in the world. Pipe fabrication and steel fabrication is abundant in Louisiana and Texas. Leadership please step up to the plate.
Agreed. At this juncture, waiting 3 weeks for the construction and deployment of domes that the company is not even sure will work seems dilatory, especially when a viable temporary solution may be available.
Howabout 2010 idea is not too far fetched. Most deepwater subsea pipelines use a suction pile to hold their subsea plets in place and as support for subsea manifolds. BP, Chevron and Shell all uses these on their other major projects. Its what holds their production rigs in place. I have seen some about 80-90 ft long and about 18-20 ft in diameter and they have two large valves on top of them already designed to be operated by ROVs. Only problem is it takes about five-eight months to fabricate them and they are so heavy it takes a heavy lift barge like the Heerema Thialf or Balder ( two largest in the world) to install them. An engineer friend and I already discussed the idea of using one of these. I was hoping he might have had some still in fabrication at either McDermotts St.Amelia yard or Kewiet’s Ingleside Texas yard. Only problem was all we had on order for the project we worked on several years ago were already installed. Other critical issue is they are not designed for a great deal of internal pressure just strong enough to withstand the suction pressure to pull them into the ocean floor and to resist bwall buckling from the pull of the chain from the subsea pipeline. The riser and junk in the well would have to be removed. Risk of open flow is probably too great. If too much pressure develops under it, it might just launch it since there will be a buoyancy effect with lighter than water oil under the pile. It could be used as a funnel for to a pipe with buoyancy to carry the oil to a series fo oceangoing barges. I wonder if there is one in service that could be removed and relocated to the BOP? Just a thought.
What he said, except you’ll need parts that are lighter and readily available. Also, you don’t have to capture all the oil at this point, just as much as you can with the tools at your disposal.
FYI
I believe these are the BP press releases referred to by kent_dreams about an hour ago:
BP 4/30:
Work is also continuing to produce a subsea collection system capable of operating in deep water to funnel leaking oil to the surface for treatment. This is expected to be ready for deployment in the next few weeks.
BP 4/29:
In parallel with these offshore efforts, advanced engineering design and fabrication of a subsea oil collection system has started onshore. This will be the first time this proven shallow water technology has been adapted for the deepwater. It is expected to be ready for deployment within the next four weeks.
I worked in the petrochemical industry 25+ years and have seen many types of leaks stopped, so I have a few suggestions that I have not seen mentioned in this post. I am aware of the depth challenge presented and the pipe size. I am a little fuzzy on just where the oil is escaping from. I realize the drill pipe, casing, whatever, etc has probably folded over the top of the BOP and kinked, but is THIS where the oil is escaping from or is it somewhere along the 5000′ of pipe probably still connected to the sunken platform?
I am not into conspiracy theories but it does strike me as more than coincidental that this rig blows right when legislation on energy policy is under review and expanded off shore drilling is finally being considered. First question I’d ask is who benefits financially and politically from this disaster and who has the means of sabotaging the rig? That should narrow the usual suspects down pretty quickly.
Next question is who is capable of conducting the independent technical investigation and inquiry necessary to determine causation and if it could or was caused by sabotage?
I note that the networks have focused primarily on the consequences and not causation or even the crew that were killed.
I am certainly not suggesting that it is sabotage but considering the enemies the United States has foreign and domestic plus the world wide interest in keeping the United States from being energy independent, a full independent criminal investigation should be carefully conducted by those skilled in engineering, accident investigation and experts in military/industrial sabotage.
OK Idea for the second time. How about a new Idea. a BOP with slip dies like the format of a dog collar. BOP would operate on HYDRAULICS. It would be like a clamp or hinged unit. It would have two sets of dies that grab one way like Dog collars do. They are capable of torquing up to 100,000 foot lb. In units called torqmasters. or Dog collars have held 100,000 lbs string weight when slips failed. This would be an ideal clamp system. This prat would not have to seal on this hinged unit. Could be attached anywhere in the casing or drill string. Next you could incorporate 2 sectional rubber donuts used on D.S.T. Conventional Packers. These would compress inside clamp BOP. next have a shear off rams then blind rams. THIs may solve the problem months ahead of schedule. Even if unit cut down the flow of oil it woudl save the environment.
Unit could be operated remotely once secure to pipe to tighten up by hydraulics. WARNING CLOSE SLOWLY.
RMARTEL.
I sent the above Idea into Nickie Scillo ( nickie.scillo@noaa.gov.)
Lets see if I hear back from these people who claim to be asking for help via the media. But seem to be hard to get a hold of.
By my calculations, a 12 Ft. diameter x 100 Ft. long cylinder fabricated from 3/16 in. steel plate would weigh in the order of 15 tons. With no pressure differentials involved 3/16 inch should be sufficient for a temporary structure such as proposed, but reinforcing rings will be required to hold the cylindrical shape. With a sufficiently large workforce the proposed cylinders could be fabricated in less than 24 hours.
I have no idea about the obstructions at the site, but if the they do not present insurmountable obstacles, a simple barrier as proposed may be effective. Possible problem: Are mile long vertically suspended suction hoses or submersible pump discharge hoses practical?
I do not see the need for a "funnel" as BP is apparently fabricating.
How About2010, thanks for the press releases regarding BP’s underwater collection efforts. What we’re discussing is a variation on the same theme – but it needs to be simpler and quicker.The PR also demonstrate that quick and decisive action is required. With so much at stake, having a possible solution ready "in a few weeks" is inadequate, especially when other low risk/cost alternatives and shortcuts might be viable. The complexity of the problem dictates the need for novel solutions that need to be implemented quickly. Keep the ideas coming.
Well they won’t put any high value vessel (Rig, Drillship, Barge Crane, etc.) over the well until it’s been killed and cemented off, the fire/explosion risk is too great. You have to remember the subsea equipment we are talking about here weighs 100s of tons altogether, just the subsea stack assy, weighs in the neighborhood of 70,000lbs, each riser joint around 10,000lbs.
I agree with subsea1, if they were circulating out the riser and the had a bad liner hanger and cement job, that could have been that camel straw, loss of hydrostatic pressure at the liner hanger caused by the loss of 5,000 feet of head from the drilling mud swap to seawater could have brought the well in. If in deed they were diverting the flow of the mud from the riser to a barge, they would not have noticed the increased flow caused by the well flowing, that detection equipment is built into the mud pits on the rig. however they should have noticed that the barge was filling at a faster rate than they were pumping seawater in, if indeed anyone was even watching it. I have witnessed this operation several times over 25 years offshore, and the usual method is to disconnect the return mud flow line at the riser slip-joint diverter and run lengths of hard 12" hose to the barge.
But that said we always installed a BOP test plug with several lengths of heavy weight drill pipe hung below it in the wellhead, and closing the blind rams when doing a temp. abandonment, be it for a storm or as a precursor to a production rig coming back to do the completion and production drilling on the rest of the field. Many deep water stacks now have a drill through production tree built into the base, which is closed and left behind when the BOP stack is retrieved after the well is secured for abandonment.
here is a link to what a BOP stack similar to this one looks like oilstatesintl.com/_filelib/ImageGallery/Products_Services…
Kent, those containers you are talking about are for surface vessel skimmers, if in fact the flow is increasing daily, this could turn into one very very large mess, the well will eventually come in full bore with unrestricted flow through a 9-5/8 casing and out through a 22" ID riser, as it displaces more and more mud from the well bore, it could flow up 30-40,000 bbls/day until the reservoir bridges off or they get a relief well done. the ideal thing to happen would be that the well "cones out" and starts producing brine instead of oil and or gas. this would depend on if this is a water driven well or gas cap driven.
About the only thing they can do presently is to light it off and burn it, to keep the mess from reaching the shoreline, place a boom barrier at right angle to the wind a place a rig to start a relief well as soon as possible.
For those thinking of lowering equipment to the seabed to recover oil as it escapes, forget it, if they could gather and assemble the necessary equipment, such as extreme deepwell pumps capable of handling the flow at 3,000psi (the static pressure at 5,000 ft of seawater is 2,200psi), the relief well would be done.
Howaboutit, the 3/16" will not work it is not strong enough to handle its own weight, it would pull itself in half. that is why drilling risers are an 1-1/4 thick.
As far as information from Transocean’s crew and or BP, we will not hear from them until the formal inquiry is over, this due to legal restrictions.
regarding verticality of the hoses/pipes and positioning equipment/ships directly over well, you might position ships just off to the side so that the hoses are more diagonal though a bit longer, if that makes a difference
One of the major problems with any type subsea recovery of the oil is the pressures and flow rates involved, 3,000psi 300gpm submersible pumps don’t grow on trees, and the high pressure load rated hoses would have to be manufactured, and shipped to the site, Coflexip and the other companies that make them don’t keep them in stock they are made to order.
At the depth we are talking about, 5,000ft everything has to be done by ROV or ALVIN type manned subs, such as used on the Titanic missions. Another problem is the weight of the equipment that needs to be lowered down, and retrieved this requires another DP drilling rig, or a very large derrick barge capable of at least 200 ton lifts with motion compensator’s and dynamic positioning, there are only a half dozen or so of these on the planet.
As far as plugging it off, there is no way to do it, the riser will not stand the pressure and there is no way to seal the drillpipe to riser annulus. One of the pictures from the USCG showed the riser bent over at the BOP stack and a leak at the kink in the riser, this leak is probably caused by the drillpipe being in the kink and caused the riser wall to crack. You have to understand that the weights involved with this equipment is beyond many folks comprehensions and it treats hardened steel like butter. As I said above just the BOP stack assy. weighs 70,000lbs.
As far as disconnecting the riser, it’s probably not currently possible, the hydraulic couplings for the choke & kill lines as well as the riser itself are in one heck of a bind because they are bent over and even if there is sufficient hydraulic pressure available to actuate the mechanisms they would probably not separate.
All of the components on the BOP stack were designed for the drill pipe & Riser to be within 10-12deg of vertical anything over that and they are put in too much mechanical bind to function properly. Besides that there are interlocks on the stack to prevent the riser disconnects from functioning unless the blind rams are closed and other safety’s are engaged, needless to say it’s not an event you want to happen on accident.
Most likely once they have the well killed and secure they will come in with ROVs and place shaped charges on the riser to cut it and the drillpipe so that BOP retrieval can begin, and the well totally plugged, and cut off at the seabed.
At 5,000ft a catenary chain and cable anchor system is almost impossible and would only be used for a very large semi permanent floating production platform because the logistics involved would be unfeasible for something like this, as the relief well would be completed before it could be implemented .
Those are all good points. However, what I’m talking about is getting 3 or 4 of the strongest pumps within a 500 mile radius (and there are probably some big ones around there) and then see what you can cobble together to mitigate. I can’t talk to the hoses, however, a nearby pipe company might have something laying around that might work and can get there in under 12.
I think a small tactical nuclear device could easily seal this well. It could cause enough debris that the well and pipe would easily be sealed. Please pass this on..
I agree with concerned citizen 2010. Use what we have available .Turn some old barges upside down and use them as the collectors with the suction pipes attached . Then we can repair the BOP or cap the well.
What about the small nuclear device…..
Halliburton or DOD. Give them a call